What Is A Truss? A truss is a structural framework composed of interconnected elements, typically arranged in triangles, designed to efficiently distribute loads and forces. At WHAT.EDU.VN, we aim to clarify engineering concepts, and this article comprehensively explores what is a truss, its components, benefits, and various types. Dive in to understand this fundamental concept and discover how trusses are critical in modern construction and structural design, focusing on truss bridge design, the different types of truss design, and truss analysis.
1. Definition and Key Characteristics of a Truss
In structural engineering, a truss is a vital structural system characterized by interconnected members forming a triangulated network. These members are arranged and connected to primarily experience axial forces. The members are often referred to as two-force members, meaning forces are applied only at their ends, resulting in either compression or tension. Trusses are favored in applications like bridge construction because of their ability to efficiently span large distances. The typical truss design showcases this structural efficiency.
The connections at the joints are typically pinned, which means they do not transfer shear or moment forces between members. This is a crucial distinction between trusses and frames. While a frame member may experience shear, axial, and bending forces, a truss member is designed to handle axial force only. This difference is fundamental in structural analysis and design.
2. Essential Components and Terminology in Truss Design
Understanding the parts of a truss is crucial for anyone studying structural engineering or construction. Here’s a breakdown of the core components and terminology related to truss structures:
2.1. Key Truss Components:
- (1) Top Chord: The uppermost beam that spans the length of the truss.
- (2) Bottom Chord: The lower beam spanning the truss’s length.
- (3) Web: The internal members that provide stability and support.
- (4) Pitching Point: The intersection where the sloping members (top chord) connect with the bottom chord.
- (5) Apex/Peak: The highest point of a truss structure.
2.2. Additional Terminology:
- Panel: A section of the truss between two adjacent vertical members.
- Node: The point where truss members intersect.
- Span: The total length covered by the truss.
- Support: The point where the truss is anchored to the ground.
- Bay: The distance between two trusses in a series.
Familiarizing yourself with these components and terms will enhance your understanding of truss structures and their applications in engineering projects. For more insights and support, visit WHAT.EDU.VN, where we provide free answers to all your queries, connecting you with knowledgeable experts. Address: 888 Question City Plaza, Seattle, WA 98101, United States. WhatsApp: +1 (206) 555-7890. Website: WHAT.EDU.VN.
3. Advantages and Benefits of Using Truss Structures
Trusses provide numerous advantages in structural design, making them ideal for various construction applications. Here are some of the key benefits:
3.1. Efficient Load Distribution
Trusses are designed to distribute loads efficiently, primarily through axial forces (tension and compression) along the truss members. This efficient distribution allows trusses to handle significant loads using minimal material.
3.2. Long Span Capability
Trusses can span long distances without intermediate support, making them ideal for bridges, large roofs, and other structures where open spaces are needed. This ability to cover long spans reduces the need for internal columns, maximizing usable space.
3.3. Material Efficiency
By utilizing axial forces, trusses minimize bending moments in the members. This allows for the use of less material compared to other structural systems, reducing costs and weight.
3.4. High Strength-to-Weight Ratio
Trusses provide a high strength-to-weight ratio, making them suitable for applications where weight is a critical factor, such as aircraft structures and portable bridges.
3.5. Versatility
Trusses can be customized to fit various shapes and sizes, making them versatile for different architectural designs. They can be used in flat, pitched, or curved configurations, adapting to diverse project requirements.
3.6. Ease of Construction
Trusses can be prefabricated off-site, allowing for faster and more efficient on-site assembly. This reduces construction time and labor costs.
3.7. Stability
The triangular geometry of trusses provides inherent stability, preventing deformation under load. This ensures the structural integrity and safety of the structure.
3.8. Cost-Effectiveness
Due to material efficiency and ease of construction, trusses offer a cost-effective solution for structural support, especially in large-span applications.
3.9. Durability
Trusses, when properly designed and maintained, can withstand environmental factors and provide long-term structural support.
3.10. Aesthetic Appeal
Trusses can be designed to be aesthetically pleasing, adding architectural interest to buildings and bridges. Exposed trusses can create a unique and visually appealing design element.
Understanding these benefits helps in appreciating why trusses are a preferred structural system in numerous engineering and construction projects. If you have more questions or need detailed insights, WHAT.EDU.VN is here to provide free answers and connect you with experts. Reach out to us at 888 Question City Plaza, Seattle, WA 98101, United States, WhatsApp: +1 (206) 555-7890, or visit our website: WHAT.EDU.VN.
4. Different Types of Trusses and Their Applications
Different truss types are designed to suit specific applications based on load requirements, span, and structural demands. Here are some common types of trusses:
4.1. Pratt Truss
The Pratt truss is characterized by vertical members in compression and diagonal members in tension. This design is efficient because steel can be reduced in diagonal members since they are under tension, which reduces cost, weight, and eases construction.
- Advantages: Cost-effective, simple design, and efficient for horizontal spans with vertical loads.
- Disadvantages: Less advantageous if the load is not primarily vertical.
- Best Used For: Cost-effective designs, a mix of loads, and simple structural requirements.
4.2. Warren Truss
The Warren truss is identified by equilateral triangles that evenly spread the load across members under a distributed load. It’s not as effective under concentrated loads because it doesn’t distribute the force evenly.
- Advantages: Even load distribution between members, fairly simple design.
- Disadvantages: Poorer performance under concentrated loads, increased construction complexity.
- Best Used For: Long-span structures and evenly distributed loads.
4.3. K Truss
The K Truss is a modification of the Pratt Truss, with shortened vertical members that improve resistance against buckling. However, members may behave unexpectedly under different load scenarios.
- Advantages: Reduced compression in vertical members, potential reduction in steel and cost.
- Disadvantages: Slightly more complex, increased construction complexity.
4.4. Howe Truss
The Howe truss is geometrically opposite to the Pratt truss. Diagonal members are in compression, while vertical loads are in tension. This truss is efficient when loaded at the bottom chord joints.
A Pratt truss (above) and a Howe Truss (below)
4.5. Fink Truss
The Fink truss features web members in a V-pattern, efficiently transmitting loads to the support. Derivatives include the Double Fink and the Fan truss types.
A Fink (top), a Double fink (middle), and a Fan Truss (bottom)
4.6. Gambrel Truss
The Gambrel truss has two different slopes, with a steeper slope from the center. It’s often used in barns to create a hollow center for storage.
Choosing the appropriate truss type is essential for maximizing structural efficiency and meeting specific project requirements. If you’re curious or have further questions, don’t hesitate to ask at WHAT.EDU.VN where we offer free consultation and answers. Contact us at 888 Question City Plaza, Seattle, WA 98101, United States, WhatsApp: +1 (206) 555-7890, or visit our website: WHAT.EDU.VN.
5. Key Applications of Trusses in Modern Engineering
Trusses are integral to many construction and engineering projects due to their strength, efficiency, and versatility. Here are some key applications:
5.1. Bridges
Trusses are commonly used in bridge construction to span long distances while supporting heavy loads. Types like Pratt, Warren, and Howe trusses are employed depending on the specific requirements of the bridge.
5.2. Roof Structures
Trusses provide efficient support for roof structures in residential, commercial, and industrial buildings. Fink and Gambrel trusses are often used in roof designs to create large, open spaces.
5.3. Aircraft Structures
Trusses are used in aircraft design to create lightweight yet strong frameworks for wings and fuselages. Their high strength-to-weight ratio is crucial in aviation.
5.4. Cranes and Lifting Equipment
Trusses form the structural framework for cranes and other lifting equipment, providing the necessary strength and stability to lift heavy loads.
5.5. Space Frames
Trusses are used in space frames to create large, open structures with minimal support. These are commonly found in exhibition halls, sports arenas, and auditoriums.
5.6. Temporary Structures
Trusses are utilized in temporary structures such as scaffolding, concert stages, and event tents. Their ease of assembly and disassembly makes them ideal for these applications.
5.7. Transmission Towers
Trusses are used in the construction of transmission towers to support power lines over long distances. Their strength and stability ensure the reliable transmission of electricity.
5.8. Offshore Platforms
Trusses provide structural support for offshore platforms, withstanding harsh marine environments and heavy loads.
5.9. Industrial Buildings
Trusses support the roofs and walls of industrial buildings, providing large, clear spans for manufacturing and storage operations.
5.10. Residential Construction
Trusses are used in residential construction to create open floor plans and support roofs. They offer a cost-effective and efficient solution for framing homes.
These applications highlight the versatility and importance of trusses in modern engineering and construction. If you’re interested in learning more or have specific questions, WHAT.EDU.VN is here to offer free assistance and connect you with experts. Contact us at 888 Question City Plaza, Seattle, WA 98101, United States, WhatsApp: +1 (206) 555-7890, or visit our website: WHAT.EDU.VN.
6. Understanding Truss Analysis Techniques
Truss analysis involves determining the forces in each member of the truss when subjected to external loads. Here are two common methods used for truss analysis:
6.1. Method of Joints
The method of joints involves analyzing each joint in the truss as a free body in equilibrium. The forces in the truss members meeting at the joint are determined using equilibrium equations (sum of forces in the x and y directions equals zero).
- Steps:
- Draw a free body diagram of each joint.
- Apply the equilibrium equations ΣFx = 0 and ΣFy = 0 at each joint.
- Solve the equations to determine the forces in the truss members.
- Identify tension (positive force) and compression (negative force) members.
6.2. Method of Sections
The method of sections involves cutting the truss into sections and analyzing one section as a free body in equilibrium. This method is useful for determining the forces in specific members without analyzing every joint.
- Steps:
- Cut the truss through the members where forces are to be determined.
- Draw a free body diagram of one section.
- Apply the equilibrium equations ΣFx = 0, ΣFy = 0, and ΣM = 0 to the section.
- Solve the equations to determine the forces in the cut members.
- Identify tension and compression members.
6.3. Matrix Method
The matrix method involves using matrix algebra to analyze the entire truss structure simultaneously. This method is suitable for complex trusses and can be implemented using computer software.
- Steps:
- Create a stiffness matrix for each truss member.
- Assemble the global stiffness matrix for the entire truss.
- Apply the boundary conditions and external loads.
- Solve the system of equations to determine the displacements and member forces.
6.4. Finite Element Analysis (FEA)
FEA is a numerical method used to analyze complex truss structures with non-linear behavior or complex loading conditions. FEA software divides the truss into small elements and solves the equations for each element to determine the overall structural behavior.
6.5. Assumptions in Truss Analysis
- Truss members are straight and slender.
- Loads are applied only at the joints.
- Joints are pinned connections (no moment transfer).
- Members are subjected to axial forces only (tension or compression).
Understanding these analysis techniques is crucial for designing safe and efficient truss structures. For more detailed explanations or if you have any questions, WHAT.EDU.VN offers free consultation and expert answers. Contact us at 888 Question City Plaza, Seattle, WA 98101, United States, WhatsApp: +1 (206) 555-7890, or visit our website: WHAT.EDU.VN.
7. Common Materials Used in Truss Construction
The selection of materials for truss construction is vital for ensuring structural integrity, durability, and cost-effectiveness. Here are some commonly used materials:
7.1. Steel
Steel is a popular choice due to its high strength, durability, and ease of fabrication. Steel trusses are used in bridges, industrial buildings, and long-span structures.
-
Advantages:
- High strength-to-weight ratio
- Good ductility and weldability
- Resistance to corrosion with proper treatment
-
Disadvantages:
- Susceptible to buckling under compression
- Higher initial cost compared to wood
7.2. Wood
Wood trusses are commonly used in residential and light commercial construction. They are cost-effective and easy to work with.
-
Advantages:
- Renewable and sustainable material
- Good strength-to-weight ratio
- Easy to cut and fasten
-
Disadvantages:
- Lower strength compared to steel
- Susceptible to decay and insect damage
- Limited span capability
7.3. Aluminum
Aluminum trusses are lightweight and corrosion-resistant, making them suitable for applications where weight is a critical factor.
-
Advantages:
- Lightweight and easy to handle
- Excellent corrosion resistance
- Good strength-to-weight ratio
-
Disadvantages:
- Lower strength compared to steel
- Higher cost than steel and wood
7.4. Concrete
Concrete trusses are used in specialized applications where high compressive strength and fire resistance are required.
-
Advantages:
- High compressive strength
- Excellent fire resistance
- Good durability
-
Disadvantages:
- Heavy and difficult to handle
- Low tensile strength
- Requires formwork for construction
7.5. Composite Materials
Composite materials such as fiber-reinforced polymers (FRP) are used in specialized applications where high strength, lightweight, and corrosion resistance are required.
-
Advantages:
- High strength-to-weight ratio
- Excellent corrosion resistance
- Design flexibility
-
Disadvantages:
- High cost
- Limited experience in structural applications
The choice of material depends on factors such as load requirements, span, environmental conditions, and cost constraints. If you need more guidance or have specific questions, WHAT.EDU.VN is ready to provide free assistance and connect you with experts. Contact us at 888 Question City Plaza, Seattle, WA 98101, United States, WhatsApp: +1 (206) 555-7890, or visit our website: WHAT.EDU.VN.
8. Common Challenges and Solutions in Truss Design
Designing truss structures involves addressing various challenges to ensure structural integrity and efficiency. Here are some common challenges and their solutions:
8.1. Buckling of Compression Members
- Challenge: Compression members in a truss are susceptible to buckling, especially if they are long and slender.
- Solution:
- Reduce the slenderness ratio by decreasing the unsupported length of the member.
- Increase the cross-sectional area or use a higher-grade material with a higher modulus of elasticity.
- Provide lateral bracing to prevent buckling in the weak direction.
8.2. Joint Stability
- Challenge: Joints in a truss must be stable and capable of transferring forces between members without failure.
- Solution:
- Use gusset plates or welded connections to ensure strong and rigid joints.
- Properly size and position the fasteners to prevent shear or tension failure.
- Design the joints to minimize eccentricity and bending moments.
8.3. Load Distribution
- Challenge: Non-uniform load distribution can lead to overstressing certain members and joints in the truss.
- Solution:
- Distribute the load evenly across the truss using bracing or load-sharing mechanisms.
- Analyze the truss under different loading scenarios to identify critical members and joints.
- Design the truss to accommodate the maximum expected loads.
8.4. Environmental Factors
- Challenge: Environmental factors such as wind, snow, and corrosion can affect the performance and durability of the truss.
- Solution:
- Design the truss to withstand wind and snow loads according to local building codes.
- Use corrosion-resistant materials or apply protective coatings to prevent corrosion.
- Provide proper drainage to prevent water accumulation and potential damage.
8.5. Material Selection
- Challenge: Selecting the appropriate material for the truss can be challenging due to factors such as cost, availability, and performance requirements.
- Solution:
- Evaluate different materials based on their strength, stiffness, durability, and cost.
- Consider the environmental conditions and potential for corrosion or degradation.
- Consult with material suppliers and structural engineers to make an informed decision.
8.6. Fabrication and Erection
- Challenge: Fabricating and erecting the truss can be complex and time-consuming, especially for large or complex structures.
- Solution:
- Use prefabricated truss components to reduce on-site labor and construction time.
- Develop a detailed erection plan to ensure safe and efficient assembly.
- Use experienced contractors and skilled labor to minimize errors and delays.
Addressing these challenges requires careful planning, analysis, and design. If you’re looking for more detailed advice or have specific questions, WHAT.EDU.VN is available to provide free support and connect you with experts. Contact us at 888 Question City Plaza, Seattle, WA 98101, United States, WhatsApp: +1 (206) 555-7890, or visit our website: WHAT.EDU.VN.
9. Innovations in Truss Design and Technology
Advancements in technology and design are continually enhancing the efficiency, sustainability, and versatility of truss structures. Here are some notable innovations:
9.1. BIM (Building Information Modeling)
- Innovation: BIM software allows engineers to create detailed 3D models of truss structures, facilitating better coordination, clash detection, and visualization.
- Benefits: Improved design accuracy, reduced errors, and enhanced collaboration among project stakeholders.
9.2. High-Strength Materials
- Innovation: The development of high-strength steel and composite materials has enabled the construction of lighter and more efficient trusses.
- Benefits: Increased span capability, reduced material usage, and improved structural performance.
9.3. Modular Construction
- Innovation: Modular construction involves prefabricating truss components off-site and assembling them on-site.
- Benefits: Reduced construction time, improved quality control, and minimized on-site disruption.
9.4. Smart Trusses
- Innovation: Smart trusses incorporate sensors and monitoring systems to track structural performance, detect damage, and provide real-time feedback.
- Benefits: Enhanced safety, improved maintenance, and extended service life.
9.5. Sustainable Design
- Innovation: Sustainable truss design focuses on using renewable materials, minimizing waste, and reducing the environmental impact of construction.
- Benefits: Reduced carbon footprint, improved energy efficiency, and enhanced sustainability.
9.6. Advanced Analysis Techniques
- Innovation: Advanced analysis techniques such as finite element analysis (FEA) and computational fluid dynamics (CFD) allow engineers to simulate complex loading conditions and optimize truss designs.
- Benefits: Improved structural performance, reduced material usage, and enhanced safety.
9.7. 3D Printing
- Innovation: 3D printing technology is being used to create complex truss components with optimized geometries and minimal waste.
- Benefits: Design flexibility, reduced material usage, and customized solutions.
These innovations are transforming the way truss structures are designed, constructed, and maintained. If you’re keen on exploring more or have specific questions, WHAT.EDU.VN is here to provide free assistance and connect you with experts. Contact us at 888 Question City Plaza, Seattle, WA 98101, United States, WhatsApp: +1 (206) 555-7890, or visit our website: WHAT.EDU.VN.
10. Frequently Asked Questions (FAQs) About Trusses
To enhance your understanding of trusses, here are some frequently asked questions along with their answers:
Question | Answer |
---|---|
What is the primary function of a truss? | A truss’s primary function is to efficiently support loads and span distances by distributing forces through a network of interconnected members, typically arranged in triangles. |
How does a truss differ from a beam? | A truss distributes loads axially (tension and compression) through its members, making it efficient for long spans. A beam primarily resists loads through bending, which may require more material for the same span. |
What are the main types of truss configurations? | The main types of truss configurations include Pratt, Warren, Howe, Fink, and Gambrel trusses, each designed for specific load conditions and structural requirements. |
What materials are commonly used in trusses? | Commonly used materials include steel, wood, aluminum, concrete, and composite materials, chosen based on factors such as strength, weight, cost, and environmental conditions. |
How is truss analysis typically performed? | Truss analysis is performed using methods such as the method of joints, method of sections, matrix method, and finite element analysis to determine the forces in each member of the truss. |
What is the significance of triangulation in trusses? | Triangulation is crucial in truss design because triangles provide inherent stability and prevent deformation under load, ensuring structural integrity. |
What are the advantages of using trusses? | Trusses offer advantages such as efficient load distribution, long span capability, material efficiency, high strength-to-weight ratio, and versatility in design. |
What is buckling in the context of trusses? | Buckling refers to the instability of compression members in a truss, where they may deform or collapse under load. This is addressed by reducing the slenderness ratio and providing lateral bracing. |
How do environmental factors affect truss design? | Environmental factors such as wind, snow, and corrosion must be considered in truss design to ensure the structure can withstand these conditions. Corrosion-resistant materials and proper drainage are used to mitigate these effects. |
What role does BIM play in modern truss design? | BIM (Building Information Modeling) allows engineers to create detailed 3D models of truss structures, improving design accuracy, reducing errors, and enhancing collaboration among project stakeholders. |
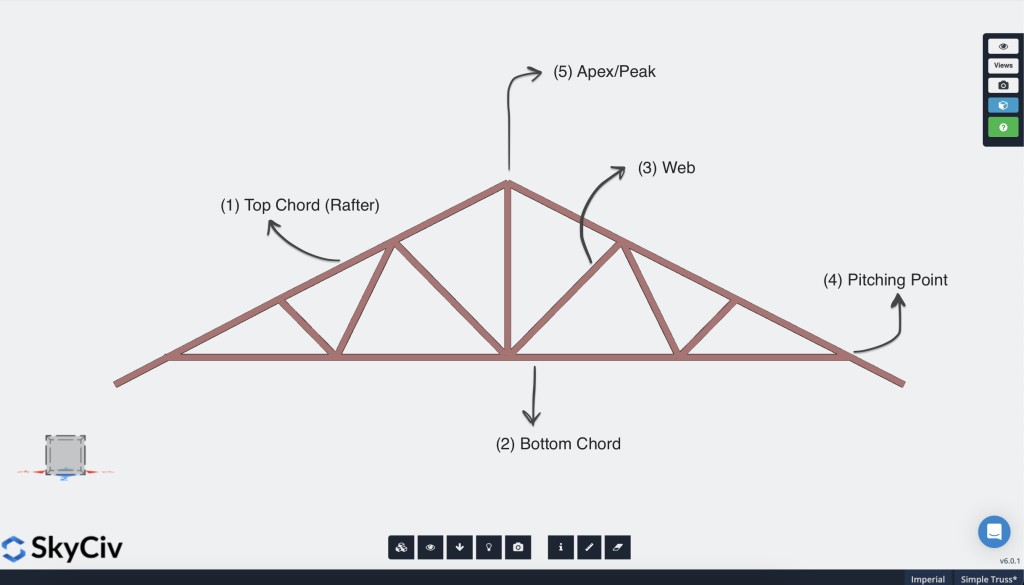
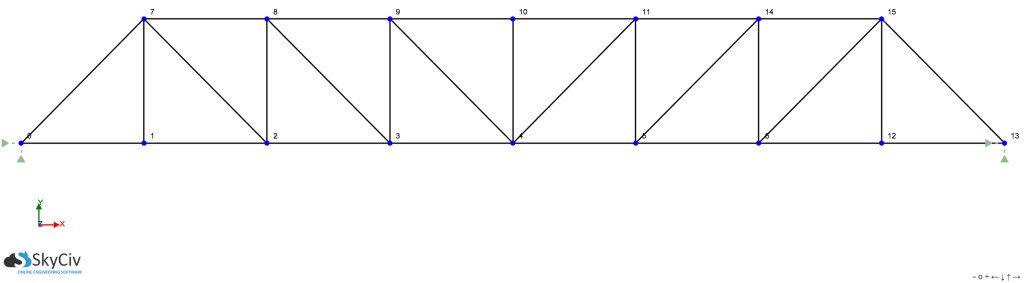
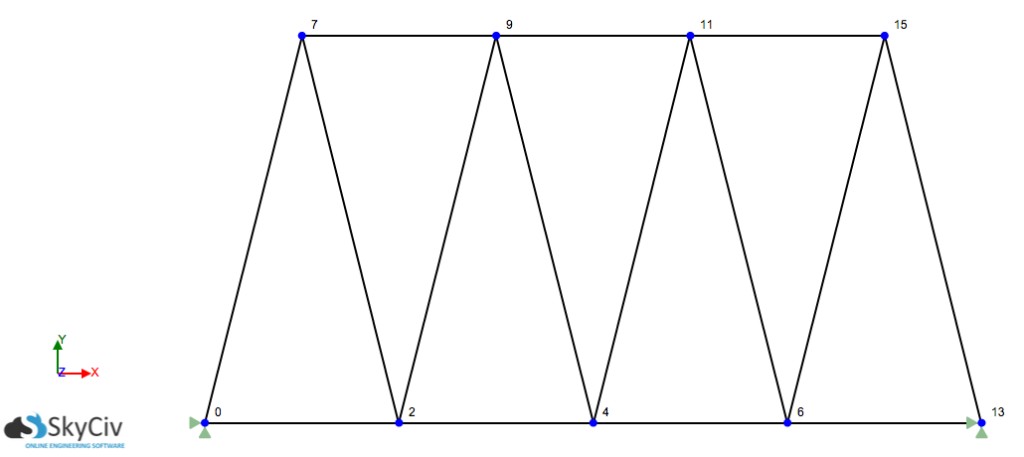
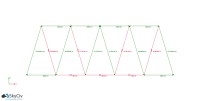
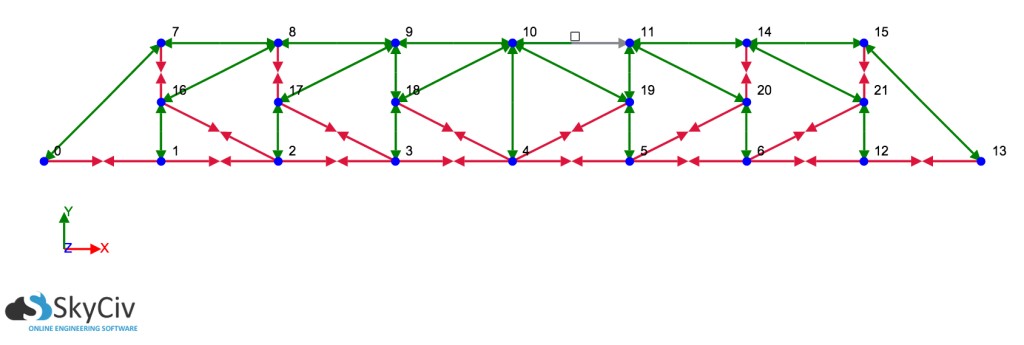
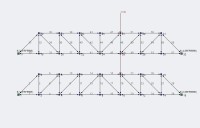
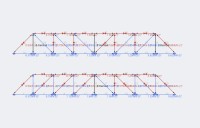
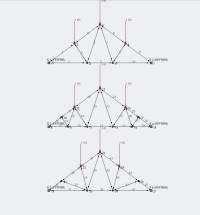
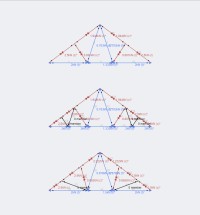
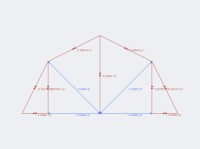
Do you have more questions or need further clarification? WHAT.EDU.VN is here to provide free answers and connect you with experts. Don’t hesitate to reach out to us at 888 Question City Plaza, Seattle, WA 98101, United States, WhatsApp: +1 (206) 555-7890, or visit our website: WHAT.EDU.VN.
Are you still curious about trusses or have more questions that need answering? Don’t hesitate! At WHAT.EDU.VN, we offer a free question-and-answer service where you can get expert insights on any topic. Whether it’s structural engineering, architectural design, or anything else, we’re here to help.
Visit WHAT.EDU.VN today and ask your question. Our community of experts is ready to provide you with the answers you need, quickly and easily. Don’t let your curiosity wait – get the information you’re looking for now. Contact us at 888 Question City Plaza, Seattle, WA 98101, United States, WhatsApp: +1 (206) 555-7890, or visit our website: what.edu.vn.