OEM, let’s explore its meaning. Uncover the core concepts of Original Equipment Manufacturers and learn how they fuel innovation across industries with WHAT.EDU.VN. Delve into the world of OEM, understanding its significance, and discover valuable insights into supplier relationships and manufacturing processes.
1. Understanding the Core: What Is Oem Mean?
The acronym OEM stands for Original Equipment Manufacturer. This term refers to a company that manufactures products or components that are then used by another company to produce its own final product. In essence, the OEM provides parts or products that are integrated into another company’s finished goods. This practice is common across diverse sectors, from automotive to technology. OEM parts are made to the specifications of the company that will ultimately sell the final product.
Think of it this way: imagine a popular laptop brand. While they assemble the final product and put their name on it, many of the internal components, such as the processor, memory, or even the screen, are manufactured by separate OEM companies. These OEMs specialize in producing those specific parts to the exact requirements of the laptop brand.
2. Diving Deeper: A Comprehensive OEM Definition
To elaborate on the fundamental “What is OEM Mean?” question, it’s useful to delve into a more comprehensive definition. OEM refers to a company that manufactures a product or component that is then purchased and rebranded by another company.
Here’s a breakdown of the key elements:
- Manufacturing Focus: OEMs are primarily focused on manufacturing. They possess the expertise, equipment, and resources to produce goods efficiently and to specific standards.
- Component or Whole Product: An OEM might produce individual components (like a car engine part) or even an entire product (like a complete computer system) for another company.
- Rebranding and Resale: The company that purchases the product from the OEM then puts its own brand name and sells the item as its own. This is a critical aspect of the OEM relationship.
- Specifications and Quality: The OEM manufactures the product according to the exact specifications and quality standards set by the purchasing company. This ensures that the final product meets the required performance and reliability criteria.
3. OEM vs. Aftermarket: Key Distinctions
When discussing OEMs, it’s crucial to understand the difference between OEM parts and aftermarket parts. This distinction affects quality, price, and warranty considerations:
Feature | OEM Parts | Aftermarket Parts |
---|---|---|
Manufacturer | Made by the original equipment manufacturer or a company contracted by the OEM. | Made by a third-party manufacturer not affiliated with the original equipment manufacturer. |
Quality | Generally considered higher quality, as they meet the exact specifications of the original part. | Quality can vary widely, and may not always meet the standards of the original part. |
Price | Typically more expensive than aftermarket parts. | Usually less expensive than OEM parts. |
Warranty | Often covered by a warranty from the original equipment manufacturer. | Warranty coverage can vary; some aftermarket parts may not come with any warranty. |
Fit and Finish | Designed for a precise fit with the original equipment. | May require modifications or adjustments to fit properly. |
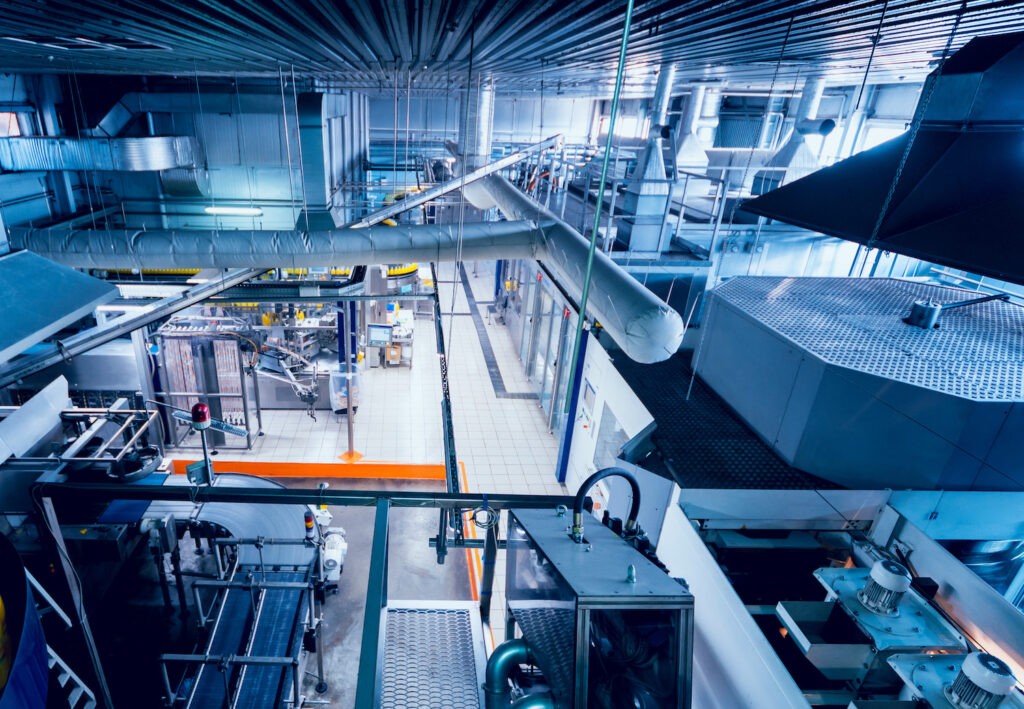
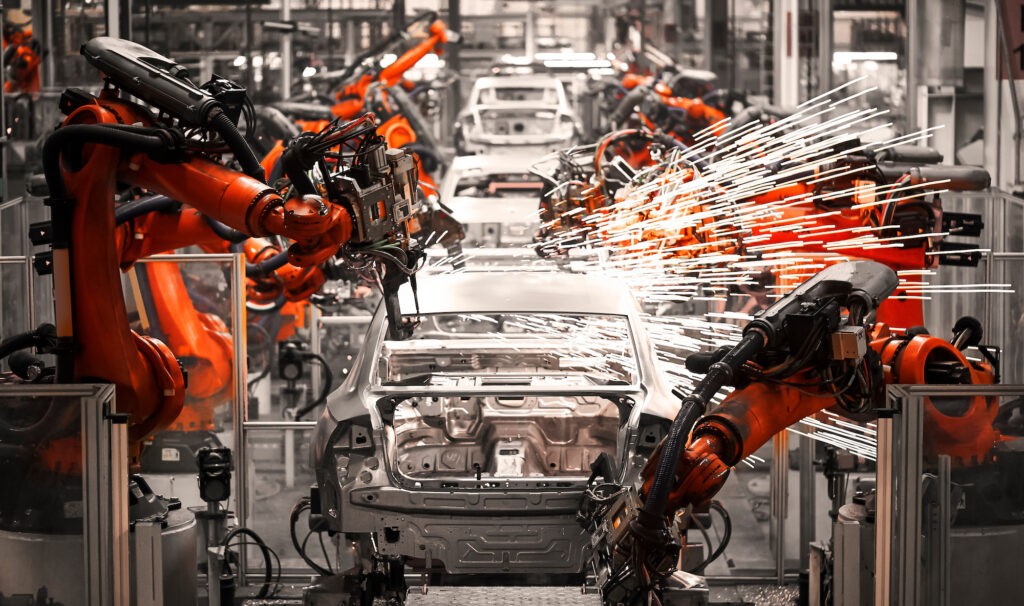
4. The Role of Value-Added Resellers (VARs)
In the OEM ecosystem, Value-Added Resellers (VARs) play a significant role. VARs are companies that add features or services to an existing product, then resell it to end-users. In the context of OEM, a VAR might purchase a product from an OEM, bundle it with their own software or services, and then sell the combined package to their customers.
For example, a company might purchase barebones computer systems from an OEM, install their own specialized software, and then sell the complete solution to businesses in a specific industry. The VAR adds value to the OEM product by providing a tailored solution that meets the unique needs of their target market.
5. Unveiling the Benefits: Why Companies Utilize OEMs
So, why do companies choose to rely on OEMs instead of manufacturing everything themselves? There are several key benefits:
- Cost Savings: Outsourcing manufacturing to OEMs can often be more cost-effective than building and operating their own manufacturing facilities. OEMs benefit from economies of scale and specialized expertise, which can translate into lower production costs.
- Focus on Core Competencies: By outsourcing manufacturing, companies can focus on their core competencies, such as product design, marketing, and sales. This allows them to allocate resources more effectively and improve their overall competitiveness.
- Access to Expertise: OEMs often possess specialized knowledge and capabilities in specific areas of manufacturing. This can provide companies with access to expertise that they may not have in-house.
- Faster Time to Market: OEMs can help companies bring new products to market faster by streamlining the manufacturing process and reducing lead times.
- Scalability: OEMs can provide companies with the flexibility to scale their production up or down as needed, without having to invest in additional manufacturing capacity.
6. OEM in the Automotive Industry: A Closer Look
The automotive industry is heavily reliant on OEMs. Car manufacturers typically source a large percentage of their components from OEMs, including engines, transmissions, electrical systems, and interior components.
Here are some examples of how OEMs operate in the automotive industry:
- Engine Manufacturers: Companies like Cummins or Caterpillar manufacture engines that are used in a variety of vehicles, from trucks to buses to construction equipment.
- Component Suppliers: Companies like Bosch or Denso supply a wide range of automotive components, including fuel injection systems, braking systems, and electronic control units.
- Tire Manufacturers: Tire companies like Michelin or Goodyear supply tires to car manufacturers for installation on new vehicles.
7. OEM in the IT and Electronics Industry
The IT and electronics industry is another major user of OEM services. Computer manufacturers, smartphone makers, and other electronics companies rely on OEMs to supply a wide range of components, including processors, memory chips, displays, and batteries.
Examples of OEM relationships in the IT and electronics industry:
- Processor Manufacturers: Companies like Intel or AMD manufacture processors that are used in computers, laptops, and servers.
- Memory Manufacturers: Companies like Samsung or Micron manufacture memory chips that are used in a variety of electronic devices.
- Display Manufacturers: Companies like LG Display or Samsung Display manufacture displays that are used in televisions, monitors, and mobile devices.
8. OEM Software: Understanding the Nuances
OEM software refers to software that is pre-installed on a new computer or other hardware device. It is typically sold at a lower price than retail versions of the software because it is bundled with the hardware. OEM software is often licensed specifically for use with the hardware it is bundled with, and may not be transferable to other devices.
Key characteristics of OEM software:
- Bundled with Hardware: Typically pre-installed on new computers or other hardware devices.
- Lower Price: Usually sold at a lower price than retail versions of the software.
- Limited Transferability: Often licensed specifically for use with the hardware it is bundled with and may not be transferable.
- Support Responsibility: The hardware manufacturer typically provides support for OEM software.
9. OEM Hardware: A Practical Perspective
OEM hardware refers to components or products that are manufactured by one company and sold to another company for use in their own products. This practice is common in industries like automotive, electronics, and manufacturing.
For example, a computer manufacturer might purchase processors from Intel (an OEM) to use in their computers. The computer manufacturer then sells the computers under their own brand name.
10. OEM vs. ODM: Untangling the Confusion
While the terms OEM and ODM are often used interchangeably, there is a key difference:
- OEM (Original Equipment Manufacturer): Manufactures products according to the specifications provided by another company. The OEM focuses on production and does not typically have its own designs.
- ODM (Original Design Manufacturer): Designs and manufactures products that are then sold to another company, which brands and sells them under its own name. The ODM is responsible for both design and manufacturing.
In essence, an OEM builds to your blueprint, while an ODM provides the blueprint and the building services.
11. Real-World OEM Examples: Illuminating the Concept
Let’s solidify our understanding of “What is OEM Mean?” with some concrete examples:
- Dell Computers: Dell sources components like processors from Intel and hard drives from Seagate. These components are OEM products that Dell integrates into their computers.
- Toyota Cars: Toyota sources various parts for their cars from different OEMs. For example, Denso supplies air conditioning systems, and Aisin Seiki provides transmissions.
- Samsung Smartphones: Samsung uses displays manufactured by Samsung Display (a related but separate entity) and processors from Qualcomm (in some models).
12. The Significance of OEM Partnerships in Manufacturing
OEM partnerships are crucial for modern manufacturing. They allow companies to:
- Specialize and Focus: Companies can focus on their core strengths, such as design, marketing, and sales, while leaving manufacturing to the experts.
- Reduce Costs: OEMs often have economies of scale and specialized expertise that can lead to lower production costs.
- Access Innovation: OEMs can provide access to new technologies and manufacturing processes.
- Improve Quality: OEMs are often highly specialized in their field, which can lead to higher quality products.
13. Navigating the Challenges of OEM Relationships
While OEM relationships offer many benefits, they also present some challenges:
- Communication: Clear and consistent communication is essential to ensure that the OEM understands the customer’s requirements and expectations.
- Quality Control: It’s important to have robust quality control processes in place to ensure that the OEM meets the required standards.
- Intellectual Property Protection: Companies need to protect their intellectual property when working with OEMs to prevent unauthorized use or disclosure.
- Supply Chain Management: Managing the supply chain effectively is crucial to ensure that the OEM can deliver products on time and within budget.
14. OEM and the Future of Manufacturing
OEM relationships are likely to become even more important in the future of manufacturing. As technology advances and global competition intensifies, companies will need to focus on their core competencies and leverage the expertise of specialized manufacturers.
OEMs can help companies:
- Adopt new technologies: OEMs are often at the forefront of technological innovation and can help companies adopt new technologies more quickly and efficiently.
- Reduce costs: OEMs can help companies reduce costs by streamlining the manufacturing process and leveraging economies of scale.
- Improve quality: OEMs are often highly specialized in their field, which can lead to higher quality products.
- Respond to changing market demands: OEMs can help companies respond to changing market demands by providing flexible and scalable manufacturing solutions.
15. Finding the Right OEM Partner: Key Considerations
Choosing the right OEM partner is critical for success. Here are some key considerations:
- Expertise: Does the OEM have the necessary expertise and experience to manufacture your product to the required standards?
- Capacity: Does the OEM have the capacity to meet your production needs, both now and in the future?
- Quality Control: Does the OEM have robust quality control processes in place?
- Communication: Is the OEM responsive and communicative?
- Cost: Is the OEM’s pricing competitive?
- Location: Is the OEM located in a convenient location for shipping and communication?
16. Maximizing Success: Best Practices for OEM Collaboration
To maximize the success of an OEM relationship, consider these best practices:
- Establish Clear Communication Channels: Maintain open and frequent communication with your OEM partner.
- Define Clear Specifications: Provide detailed and unambiguous specifications for your product.
- Implement Robust Quality Control: Establish a comprehensive quality control program to monitor the OEM’s performance.
- Build a Strong Relationship: Foster a collaborative and trusting relationship with your OEM partner.
- Regularly Review Performance: Periodically review the OEM’s performance and identify areas for improvement.
17. How ToolSense Can Enhance OEM Operations
ToolSense offers solutions that can improve various aspects of OEM operations, enabling businesses to effectively oversee their equipment and assets, streamline processes, and make data-driven decisions.
Here are specific ways ToolSense can be applied:
- Equipment Maintenance & Tracking: Improve maintenance schedules to reduce downtime and increase the lifespan of manufacturing tools.
- Inventory Management: Implement inventory control systems to avoid stockouts and overstocking of parts and components.
- Compliance and Safety: Maintain equipment in line with health and safety regulations, reducing risks and possible penalties.
- Data Analysis: Analyze equipment performance metrics for process optimization and cost reduction.
By using ToolSense, OEM companies can enhance productivity, reduce operational expenses, and enhance overall equipment efficiency, leading to increased profits and better customer satisfaction.
18. OEM in the Hospitality Industry
The hospitality sector relies on OEMs for a wide range of products, from furniture and fixtures to linens and kitchen equipment. Hotels, restaurants, and other hospitality businesses often outsource the manufacturing of these items to OEMs to save costs and ensure consistent quality.
Examples of OEM products used in the hospitality industry:
- Furniture: Beds, chairs, tables, and other furniture items.
- Linens: Towels, sheets, and tablecloths.
- Kitchen Equipment: Ovens, refrigerators, and dishwashers.
- Amenities: Soaps, shampoos, and lotions.
19. Original Equipment Manufacturer Example in the Electronics and IT Industry
In the fast-paced electronics and IT sector, OEMs are crucial for efficient manufacturing and innovation. Companies frequently outsource the production of computer parts and software to OEMs to cut costs and ensure high standards.
Common examples include:
- CPUs and GPUs: Outsourcing the production of processors and graphic cards to specialized manufacturers.
- Software Bundling: Pre-installing software on computers by partnering with software developers.
- Displays and Batteries: Sourcing displays and batteries for smartphones and tablets from dedicated OEMs.
20. Embracing Efficiency: The OEM Advantage
OEMs offer numerous advantages, enabling businesses to maximize their efficiency and success:
- Focus on Core Competencies: Concentrate on product design, marketing, and sales while outsourcing manufacturing.
- Reduce Costs: Benefit from economies of scale and specialized expertise, resulting in lower production costs.
- Access Expertise: Tap into specialized knowledge and capabilities in specific areas of manufacturing.
- Faster Time to Market: Streamline the manufacturing process and reduce lead times to bring new products to market faster.
- Scalability: Scale production up or down as needed without investing in additional manufacturing capacity.
Still using pen & paper to track your equipment? Get our free ToolSense Equipment Management Sheet
21. Answering Your Questions: OEM FAQs
Let’s address some frequently asked questions about OEMs:
- What Does OEM Mean? OEM stands for Original Equipment Manufacturer, a company that produces products or components for another company to sell under its own brand.
- What Is an Example of an OEM? An example of an OEM (Original Equipment Manufacturer) is a company that produces components or products that are used in another company’s end products. For instance, a computer manufacturer may source OEM components like processors, motherboards, or hard drives from various OEMs and integrate them into their final product.
- Does OEM Mean Fake? No, OEM does not mean fake. OEM refers to the original equipment manufacturer, which is a company that produces components or products for use in other companies’ end products. These components are often of high quality and meet the specifications the purchasing company requires. While OEM products may not carry the branding of the purchasing company, they are genuine and legitimate products provided by authorized manufacturers.
- What Is OEM and ODM? Original equipment manufacturer (OEM) stands for companies that carry out bulk productions, while original design manufacturer (ODM) stands for the company that designed the product.
22. Concluding Thoughts: The Power of OEM
In conclusion, understanding “What is OEM Mean?” is essential for navigating the complexities of modern manufacturing and supply chain management. OEMs play a critical role in helping companies reduce costs, focus on their core competencies, and bring new products to market faster. By carefully selecting and managing OEM partners, businesses can unlock significant advantages and achieve greater success.
Unlock your potential with what.edu.vn. Any questions? We provide free answers. If you have questions, please contact us. Our address is 888 Question City Plaza, Seattle, WA 98101, United States. Whatsapp: +1 (206) 555-7890.