What Is Paper Made Of? At WHAT.EDU.VN, we break down the paper-making process, from sourcing fibers to creating the final product, offering clear and easy-to-understand explanations. Discover the fascinating world of paper production and never hesitate to ask any question you have at WHAT.EDU.VN to get the most reliable and helpful answers.
1. Unveiling the Basic Components: What Goes Into Paper?
Paper, a ubiquitous material in our daily lives, has a surprisingly diverse origin. The primary ingredient is cellulose fibers, but where do these fibers come from? Understanding the sources of these fibers is key to understanding what paper is made of.
1.1. Wood Pulp: The Dominant Source
The vast majority of paper is derived from wood pulp. This pulp is obtained from various tree species, both softwood and hardwood.
- Softwood trees: These include species like spruce, pine, fir, larch, and hemlock. They are favored for their long fibers, which contribute to the strength and tear resistance of paper.
- Hardwood trees: Examples include eucalyptus, aspen, and birch. Hardwood fibers are shorter, resulting in paper with a smoother surface and better printability.
1.2. Beyond Trees: Alternative Fiber Sources
While wood is the primary source, paper can also be made from other natural fibers, each imparting unique characteristics to the final product.
- Cotton: Cotton fibers are exceptionally strong and durable, making cotton paper ideal for archival documents, letterheads, and other high-end stationery. The distinctive feel and luxurious quality of cotton paper make it a preferred choice for applications demanding elegance and longevity.
- Other Plant Fibers: These include hemp, flax, kenaf, and bamboo. These alternative fibers are gaining popularity due to their sustainability and unique properties. Hemp, for instance, produces strong and durable paper, while bamboo offers rapid renewability.
1.3. Recycled Fibers: Giving Paper a Second Life
In an effort to conserve resources and reduce waste, recycled fibers are increasingly incorporated into paper production. These fibers come from two main sources:
- Pre-consumer waste: This includes paper scraps and trimmings generated during the paper manufacturing and printing processes.
- Post-consumer waste: This consists of paper products that have already been used by consumers, such as recycled newspapers, magazines, and office paper.
1.4. Additives: Enhancing Paper Properties
In addition to the primary fiber source, various additives are incorporated during the paper-making process to enhance specific properties, such as:
- Fillers: These improve the paper’s opacity, brightness, and smoothness. Common fillers include clay, calcium carbonate, and titanium dioxide.
- Sizing agents: These control the paper’s absorbency, preventing ink from feathering or bleeding.
- Dyes and pigments: These add color to the paper.
- Strengthening agents: These improve the paper’s tensile strength and tear resistance.
2. From Fiber to Pulp: The Pulping Process Explained
Once the fiber source is determined, the next step is to convert it into pulp, a slurry of individual fibers suspended in water. There are two main pulping methods: mechanical and chemical.
2.1. Mechanical Pulping: A High-Yield Approach
Mechanical pulping involves grinding wood logs into fibers using a rotating disk or stone. This process is relatively inexpensive and produces a high yield of pulp, meaning that a large proportion of the wood is converted into usable fibers.
- Process: Logs are fed into a grinder where they are pressed against a rotating abrasive surface, such as a stone or a metal disk. The friction breaks down the wood into individual fibers.
- Characteristics: Mechanical pulp contains both whole and fragmented fibers, as well as lignin, a complex polymer that binds the fibers together in wood. Lignin gives the paper a yellowish or grayish color and makes it more prone to yellowing and degradation over time.
- Applications: Mechanical pulp is commonly used to produce newsprint, paperboard, and other low-cost paper products.
2.2. Chemical Pulping: Removing Lignin for Higher Quality
Chemical pulping involves treating wood chips with chemicals to dissolve the lignin, leaving behind the cellulose fibers. This process produces a higher quality pulp that is brighter, stronger, and more durable than mechanical pulp.
- Process: Wood chips are cooked in a chemical solution, such as kraft (sulfate) or sulfite, at high temperatures and pressures. The chemicals dissolve the lignin, separating the fibers.
- Characteristics: Chemical pulp is composed of relatively pure cellulose fibers with minimal lignin content. This results in paper that is brighter, smoother, and more resistant to yellowing.
- Applications: Chemical pulp is used to produce a wide range of paper products, including printing and writing papers, packaging materials, and specialty papers.
2.3. A Comparison of Mechanical and Chemical Pulping
Feature | Mechanical Pulping | Chemical Pulping |
---|---|---|
Fiber Yield | High (95%) | Lower (40-50%) |
Lignin Content | High | Low |
Fiber Quality | Lower | Higher |
Brightness | Lower | Higher |
Strength | Lower | Higher |
Cost | Lower | Higher |
Environmental Impact | Higher energy consumption, more waste | Lower energy consumption, less waste |
Applications | Newsprint, paperboard | Printing papers, packaging materials |
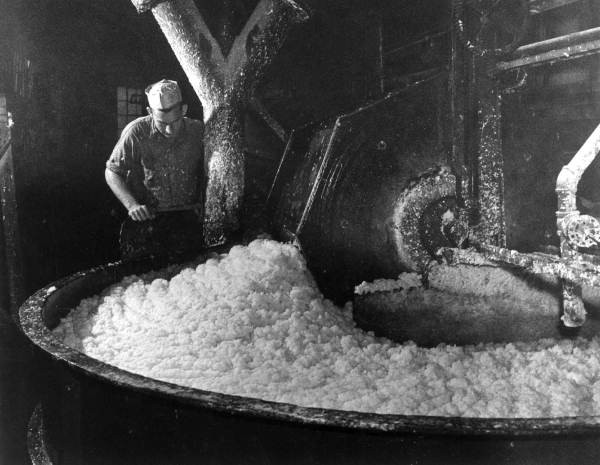
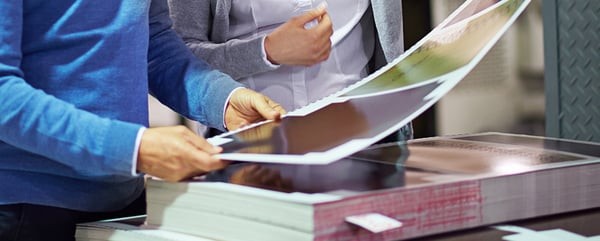
3. The Paper-Making Machine: From Pulp to Sheet
Once the pulp is prepared, it is fed into a paper-making machine, a complex piece of machinery that transforms the pulp into a continuous sheet of paper. The paper-making machine consists of four main sections: the wet end, the press section, the dryer section, and the calender section.
3.1. The Wet End: Forming the Sheet
The wet end is where the pulp slurry is deposited onto a moving wire mesh. As the water drains away, the fibers begin to interlock, forming a web.
- Process: The pulp slurry is sprayed onto the moving wire mesh, also known as the forming fabric. The water drains through the mesh, leaving behind a mat of fibers.
- Grain Direction: The orientation of the fibers on the wire mesh determines the grain direction of the paper. Paper has a grain direction, meaning it is stronger and folds more easily in one direction than the other.
3.2. The Press Section: Removing More Water
The web of fibers then passes through a series of rollers in the press section, which squeeze out more water and compact the fibers.
- Process: The web is passed between a series of rollers, which apply pressure to remove water. The water is absorbed by felt blankets that surround the rollers.
- Felt Blankets: The felt blankets help to absorb water and provide a smooth surface for the paper to travel over.
3.3. The Dryer Section: Evaporating the Remaining Moisture
The paper then enters the dryer section, where it passes over a series of heated rollers that evaporate the remaining moisture.
- Process: The paper is passed over a series of heated rollers, which dry the paper. The temperature of the rollers is carefully controlled to prevent the paper from becoming too dry or brittle.
- Felt Blankets: Felt blankets are also used in the dryer section to help hold the paper against the heated rollers and to absorb moisture.
3.4. The Calender Section: Smoothing the Surface
Finally, the paper passes through the calender section, where it is pressed between a series of smooth rollers to create a smooth, uniform surface.
- Process: The paper is passed between a series of smooth rollers, which compress the fibers and create a smooth surface.
- Gloss and Finish: The number and pressure of the rollers in the calender section determine the gloss and finish of the paper.
4. Specialty Papers: Coatings and Finishes
To achieve specific properties, such as gloss, water resistance, or printability, paper can be coated with various substances.
4.1. Coated Papers: Enhancing Print Quality
Coated papers have a layer of coating applied to one or both sides. This coating improves the paper’s smoothness, gloss, and ink receptivity, resulting in sharper, more vibrant images and text.
- Types of Coatings: Common coatings include clay, calcium carbonate, and synthetic polymers.
- Applications: Coated papers are used for magazines, brochures, catalogs, and other high-quality print materials.
4.2. Uncoated Papers: A Natural Look and Feel
Uncoated papers lack a coating layer and have a more natural look and feel. They are often preferred for applications where readability and tactile experience are important.
- Characteristics: Uncoated papers are more absorbent than coated papers, making them suitable for writing and drawing.
- Applications: Uncoated papers are used for books, stationery, and envelopes.
4.3. Supercalendering: Creating a Glossy Finish
Supercalendering is a process that involves passing paper through a series of highly polished rollers that rotate at different speeds. This process creates a smooth, glossy surface without the need for a coating.
- Process: The paper is passed between a series of rollers, some of which are heated and some of which are cooled. The rollers rotate at different speeds, creating friction that polishes the paper surface.
- Applications: Supercalendered paper is used for magazines, catalogs, and other print materials where a glossy finish is desired.
5. The Environmental Impact of Paper Production
Paper production can have a significant environmental impact, including deforestation, water pollution, and greenhouse gas emissions. However, sustainable practices are being implemented to mitigate these impacts.
5.1. Sustainable Forestry Practices
Sustainable forestry practices aim to manage forests in a way that meets the needs of the present without compromising the ability of future generations to meet their own needs.
- Reforestation: Planting new trees to replace those that are harvested.
- Selective Logging: Harvesting only mature trees, leaving younger trees to grow.
- Reduced-Impact Logging: Using techniques that minimize damage to the forest ecosystem.
5.2. Recycling and Waste Reduction
Recycling paper reduces the demand for virgin wood pulp, conserving forests and reducing waste.
- Recycled Content: Choosing papers with a high percentage of recycled content.
- Reducing Paper Consumption: Using paper more efficiently and reducing waste.
5.3. Cleaner Production Technologies
Cleaner production technologies aim to reduce the environmental impact of paper production by minimizing water and energy consumption, reducing pollution, and using more sustainable materials.
- Closed-Loop Systems: Recycling water and chemicals used in the paper-making process.
- Renewable Energy: Using renewable energy sources, such as solar and wind power, to power paper mills.
- Alternative Fibers: Using alternative fibers, such as hemp and bamboo, which require less water and energy to produce than wood pulp.
6. FAQ: Your Burning Questions About Paper Answered
Here are some frequently asked questions about what paper is made of:
Question | Answer |
---|---|
What are the main types of paper? | Common types include printing paper, writing paper, newsprint, packaging paper, and specialty papers like photo paper and cardstock. |
Is all paper made from trees? | No, paper can also be made from cotton, hemp, bamboo, and recycled materials. |
What is the difference between coated and uncoated paper? | Coated paper has a surface coating for better print quality, while uncoated paper has a more natural texture. |
How does recycling help the environment? | Recycling reduces the need for virgin wood pulp, conserving forests and reducing landfill waste. |
What is “paper grain”? | Paper grain refers to the direction in which most fibers are aligned, affecting its folding and tearing properties. |
What is lignin? | Lignin is a complex polymer in wood that is removed during chemical pulping to produce brighter, stronger paper. |
How is paper made glossy? | Glossy paper is achieved through coatings or a process called supercalendering. |
What are the environmental impacts of paper production? | Impacts include deforestation, water pollution, and greenhouse gas emissions, but sustainable practices can mitigate these. |
Is paper biodegradable? | Yes, paper is biodegradable, but the rate of decomposition depends on environmental conditions. |
How can I make paper at home? | You can make paper at home by blending recycled paper with water, forming a pulp, and pressing it into a sheet. |
7. Still Have Questions? Ask WHAT.EDU.VN!
Understanding what paper is made of involves exploring its various components, from fiber sources to additives, and the complex processes that transform these materials into the paper we use every day. From the types of wood used, to the chemical processes that provide us with bright, durable paper, there is so much to know. Whether it’s the different types of pulp or the environmental impact of paper production, we’ve covered the main areas here.
Do you still have questions about paper or any other topic? Don’t hesitate to ask the community at WHAT.EDU.VN for free! Our platform is designed to provide you with quick, accurate, and helpful answers from knowledgeable individuals.
Have a question? Get free answers now at WHAT.EDU.VN!
Contact us:
- Address: 888 Question City Plaza, Seattle, WA 98101, United States
- WhatsApp: +1 (206) 555-7890
- Website: what.edu.vn