Six Sigma is more than just a buzzword in the business world; it’s a powerful, data-driven methodology aimed at process improvement and defect reduction. Originating from Motorola in the 1980s, Six Sigma has evolved into a globally recognized standard for organizations striving for operational excellence. Companies like General Electric, Toyota, and Amazon have successfully adopted Six Sigma principles to enhance customer satisfaction, streamline operations, and boost profitability across diverse sectors, from manufacturing to healthcare, finance, and services.
Boost your expertise: Consider elevating your career trajectory with a Certified Lean Six Sigma Green Belt certification. Enroll today to begin your journey towards mastering process improvement techniques! 🎯
To grasp the essence of Six Sigma, let’s delve deeper into its definition, principles, methodologies, and practical applications.
Decoding Six Sigma: Definition and Core Principles
At its heart, What Is Six Sigma? Six Sigma is a rigorous, data-centric approach to improving business processes. It works by minimizing errors and defects, reducing process variability, and enhancing overall quality and efficiency. The ultimate goal of Six Sigma is to achieve near perfection in process output, statistically aiming for just 3.4 defects per million opportunities.
This ambitious target is achieved through a structured, step-by-step methodology known as DMAIC (Define, Measure, Analyze, Improve, Control). DMAIC provides a roadmap for identifying the root causes of process variation and systematically eliminating them, leading to significant process improvements.
Six Sigma is inherently linked to project management, providing a robust framework for minimizing deviations that can negatively impact project timelines, budgets, and deliverables. It’s a disciplined and quantifiable approach to problem-solving and process optimization.
The term “Six Sigma” itself is rooted in statistics. The Greek letter sigma (σ) represents standard deviation, a measure of process variability. In a normal distribution or bell curve, one sigma indicates a certain level of deviation from the mean. A Six Sigma process implies that the process mean is at least six standard deviations away from the nearest specification limit. This translates to an extremely low defect rate, as illustrated in the normal distribution curve:
Alt: Normal distribution curve visually representing Six Sigma methodology and defect rate reduction.
This graph visually emphasizes the statistical foundation of the Six Sigma model. Higher standard deviation indicates a wider spread of values. Six Sigma aims for processes where the mean is far removed from specification limits, minimizing the chance of defects.
Lean Six Sigma: Synergizing Efficiency and Quality
Often discussed alongside Six Sigma is Lean Six Sigma. This powerful methodology integrates the principles of Lean manufacturing with Six Sigma, creating a comprehensive approach to process excellence.
Lean principles focus on waste reduction and efficiency maximization. It’s about identifying and eliminating activities that don’t add value to the customer, streamlining workflows, optimizing resource utilization, and improving quality through waste elimination.
Six Sigma, on the other hand, provides the statistical rigor for reducing variation and defects. It emphasizes data-driven decision-making within the DMAIC framework to achieve consistent and predictable process outcomes.
By combining Lean and Six Sigma, Lean Six Sigma offers a holistic toolkit for process improvement applicable across industries. It’s particularly effective in sectors like manufacturing, healthcare, finance, and service industries, driving efficiency gains, cost reductions, and enhanced customer experiences.
Further Reading: Explore Six Sigma Certification: All You Need to Know to understand the benefits of certification.
The Foundational 5 Principles of Six Sigma
The core philosophy of Six Sigma centers around delivering near-perfect products and services to achieve optimal customer satisfaction and drive business transformation. This is accomplished through a dual approach grounded in five fundamental principles:
These principles are the bedrock of any successful Six Sigma implementation:
-
Customer-Centric Focus: Echoing the adage “the customer is king,” this principle prioritizes maximizing customer benefit. Organizations must deeply understand their customers’ needs, expectations, and drivers of loyalty. Defining quality standards from the customer’s perspective is paramount.
-
Data-Driven Approach: Six Sigma emphasizes measurable data and facts to drive decision-making, rather than assumptions or guesswork. This involves meticulously mapping processes to identify waste areas and collecting relevant data to pinpoint problem areas. Clear goals for data collection are crucial, including defining data types, purpose, expected insights, accuracy, and standardized collection systems.
-
Process Improvement and Variation Reduction: Once problem areas are identified through data analysis, the focus shifts to process improvement. This involves implementing changes to eliminate variations and defects. Activities that don’t contribute to customer value are removed, streamlining processes for enhanced quality and efficiency.
-
Teamwork and Collaboration: Six Sigma success relies on the collective expertise and collaboration of stakeholders across different levels and departments. A structured approach encourages team contributions and leveraging diverse expertise for effective problem-solving. Specialized training in Six Sigma principles and methodologies ensures team proficiency and minimizes project risks.
-
Continuous Improvement and Adaptability: Six Sigma is not a one-time fix but an ongoing journey of business transformation and adaptation. A culture of flexibility and responsiveness to process changes is essential. Organizations must continuously monitor data, analyze performance metrics, and adapt processes as needed to maintain a competitive edge and ensure seamless project implementation.
Six Sigma Methodologies: DMAIC and DMADV
Two primary methodologies form the backbone of Six Sigma: DMAIC and DMADV. Each provides a structured roadmap for process improvement and business transformation, tailored to different scenarios.
DMAIC (Define, Measure, Analyze, Improve, Control) is a data-driven, iterative methodology focused on improving existing processes or products for enhanced customer satisfaction. It’s the most widely used Six Sigma methodology, particularly applicable to manufacturing and service delivery.
DMADV (Define, Measure, Analyze, Design, Verify), part of the Design for Six Sigma (DFSS) framework, is used for designing new processes, products, or services, or re-designing existing ones that don’t meet customer needs even after optimization. DMADV is employed when a completely new approach is required.
Methodology | Focus | Application | Key Phases |
---|---|---|---|
DMAIC | Improving existing processes | Manufacturing, Service Delivery | Define, Measure, Analyze, Improve, Control |
DMADV | Designing new processes/products | Product Development, Process Redesign | Define, Measure, Analyze, Design, Verify |
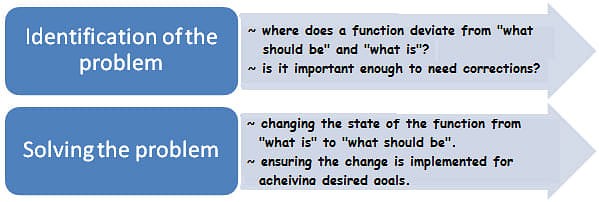

Professionals aiming to master Six Sigma methodologies often pursue certification programs to gain in-depth knowledge and practical skills in applying DMAIC and DMADV across diverse business contexts.
The DMAIC Process: A Step-by-Step Approach to Business Transformation
While Six Sigma encompasses various problem-solving methods, DMAIC stands out as the standard methodology for practitioners. It’s a data-driven management process focused on optimizing and improving business processes through a strong customer focus and rigorous use of data and statistics.
The Six Sigma DMAIC process unfolds in five distinct phases:
-
DEFINE: This initial phase sets the stage by clearly defining the problem from the customer’s perspective.
- Step 1: Define the business problem statement from the customer’s viewpoint.
- Step 2: Establish clear, measurable goals. What needs to be achieved? What resources are available?
- Step 3: Map the current process and validate understanding with stakeholders.
-
MEASURE: The focus shifts to quantifying the problem and establishing reliable metrics.
- Step 1: Quantify the problem using data and numerical measures.
- Step 2: Define performance standards and establish limits for key metrics (“Y”).
- Step 3: Evaluate the measurement system to ensure accuracy and reliability in data collection.
-
ANALYZE: This phase delves into data analysis to identify root causes and key influencing factors.
- Step 1: Assess process efficiency and effectiveness in achieving desired outcomes.
- Step 2: Quantify improvement goals numerically (e.g., reduce defects by 20%).
- Step 3: Analyze historical data to identify patterns and variations.
-
IMPROVE: Solutions are developed and implemented to address root causes and improve process performance.
- Step 1: Brainstorm and identify potential solutions and root causes (“X” variables impacting “Y”).
- Step 2: Test and validate the relationship between key variables and process outcomes.
- Step 3: Establish process tolerances – acceptable ranges for variables to maintain desired quality and performance. Tools like robust optimization can be employed.
-
CONTROL: The final phase ensures that implemented improvements are sustained over time.
- Step 1: Validate the measurement system for ongoing monitoring.
- Step 2: Establish process capability – assess if goals are being consistently met (e.g., defect reduction target).
- Step 3: Implement process controls and monitoring systems to maintain improvements.
Key Six Sigma Techniques: Tools for Process Excellence
The Six Sigma toolkit includes a blend of statistical analysis, data visualization, and qualitative techniques to drive process improvement.
Here are some essential Six Sigma techniques:
-
Brainstorming: A fundamental technique for generating ideas and creative solutions, often used in the “Improve” phase of DMAIC. Facilitated group discussions encourage free-flowing idea generation to approach problems from multiple angles.
-
Root Cause Analysis / 5 Whys: This technique, crucial in the “Analyze” phase, helps drill down to the fundamental causes of problems. By repeatedly asking “why?” (often five times), the underlying issue is uncovered.
-
Voice of the Customer (VOC): A process for capturing customer feedback (both internal and external) to align products and services with customer needs and expectations. VOC is vital in the “Define” phase to ensure problem definition is customer-centric.
-
5S System: Originating from Japanese workplace practices, 5S focuses on workplace organization and efficiency. The five steps are: Sort (Seiri), Set in Order (Seiton), Shine (Seiso), Standardize (Seiketsu), and Sustain (Shitsuke). It eliminates waste and bottlenecks from inefficient workplace layouts and resource management.
-
Kaizen (Continuous Improvement): A philosophy of ongoing, incremental improvement. Kaizen involves continuously monitoring processes, identifying areas for improvement, and implementing changes, especially valuable in manufacturing settings for waste reduction and efficiency gains.
-
Benchmarking: A technique for comparing an organization’s processes and performance against industry best practices or competitors. Benchmarking can be internal (comparing departments), functional (comparing functions with industry leaders), or competitive (comparing products/services with competitors).
-
Poka-yoke (Mistake-Proofing): Japanese for “error prevention,” poka-yoke techniques aim to prevent errors from occurring in the first place, particularly during manufacturing processes. It involves designing processes to make errors impossible or easily detectable.
-
Value Stream Mapping: A visual tool that maps the flow of materials and information in a process to identify waste and inefficiencies. It helps design future-state processes with leaner operations by highlighting seven types of waste and waste removal opportunities.
Essential Six Sigma Tools
Beyond techniques, specific tools are employed within Six Sigma methodologies:
-
Cause and Effect Analysis (Fishbone Diagram): Visualizes potential causes of a problem, categorizing them for structured analysis.
-
Flow Chart: Diagrammatically represents process steps, aiding in understanding process flow and identifying bottlenecks.
-
Pareto Chart: A bar chart that prioritizes problem areas based on frequency or impact, following the Pareto principle (80/20 rule).
-
Histogram: Graphical representation of data distribution, showing frequency of data values within defined ranges.
-
Check Sheet: A structured form for collecting and organizing data systematically, often used for tracking defects or occurrences.
-
Scatter Plot: Graphically displays the relationship between two variables to identify potential correlations.
-
Control Chart: Tracks process performance over time, identifying variations and deviations from control limits to ensure process stability.
Six Sigma Certification Levels: Belts of Expertise
Six Sigma certification follows a belt system, similar to martial arts, indicating increasing levels of knowledge and expertise.
Alt: Pyramid diagram illustrating the five Six Sigma certification levels: White Belt, Yellow Belt, Green Belt, Black Belt, Master Black Belt.
-
White Belt: Entry-level, basic understanding of Six Sigma concepts, participates in problem-solving teams.
-
Yellow Belt: Project team member, reviews process improvements, understands methodologies and DMAIC.
-
Green Belt: Requires 3+ years of work experience, understands tools and methodologies, leads Green Belt projects, assists Black Belts.
-
Black Belt: Requires 3+ years of experience, core knowledge area expertise, leads complex projects, trains teams.
-
Master Black Belt: Highest level, requires Black Belt certification, extensive experience (5+ years, 10+ projects), coaches other belts, develops metrics and strategies, organizational advisor.
Become a Certified Professional: Explore Six Sigma training options to advance your career.
Career Paths and Salary Expectations in Six Sigma
Six Sigma expertise is highly valued across diverse industries, creating numerous career opportunities with competitive salaries.
-
Six Sigma Consultant: Advises organizations on process improvement, cost reduction, and strategy implementation. Average salary: ~$96,000/year.
-
Six Sigma Project Manager: Manages Six Sigma projects, leads teams, ensures successful implementation. Average salary: ~$107,000/year.
-
Six Sigma Black Belt: Leads complex projects, trains teams, drives sustained improvements. Average salary: ~$110,000/year.
-
Six Sigma Master Black Belt: Leads organizational initiatives, mentors Black and Green Belts, drives business transformation. Average salary: ~$140,000/year.
-
Quality Manager: Ensures product/service quality meets standards. Six Sigma certification is a valuable asset. Average salary: ~$91,000/year.
Six Sigma certification can significantly enhance career prospects and earning potential. Individuals with certification often command higher salaries and have better job opportunities.
Ready to take the next step? Enroll in our Lean Six Sigma Green Belt Certification Training and begin your journey to operational excellence. 🎯
Resources for Six Sigma Learning
Whether you are a recent graduate, engineer, or MBA professional, Six Sigma certification can be a valuable asset for career advancement. Starting with a Green Belt certification and progressing to higher levels can significantly boost your earning potential. Simplilearn’s Green Belt certificate program offers a great starting point for learning Six Sigma principles and advancing your career in quality management.
Frequently Asked Questions (FAQs) about Six Sigma
1. How Can You Get Six Sigma Certification?
The path to Six Sigma certification involves understanding your organization’s approach, choosing between Six Sigma and Lean Six Sigma, determining the appropriate belt level, learning about certification exams, enrolling in training, and obtaining your certification.
2. What Does Six Sigma Mean?
Six Sigma is a quality improvement methodology focused on minimizing defects in processes to enhance business performance and profitability.
3. What Is the Difference Between Six Sigma and Lean Six Sigma?
Lean focuses on waste reduction across the organization, while Six Sigma emphasizes defect reduction through statistical methods. Lean Six Sigma combines both approaches for a comprehensive improvement strategy.
4. What Are the Steps of Six Sigma?
The core steps of Six Sigma follow the DMAIC methodology: Define, Measure, Analyze, Improve, and Control.
5. What is Lean Six Sigma?
Lean Six Sigma is a collaborative, team-based methodology for improving performance by systematically eliminating waste and reducing process variation.
6. What is continuous improvement?
Continuous improvement, often called Kaizen or rapid improvement, is a Lean technique focused on ongoing workflow optimization to save time and resources.
7. What is Lean Six Sigma Yellow Belt?
A Lean Six Sigma Yellow Belt has a foundational understanding of Six Sigma and supports project teams, often contributing to process mapping.
8. What is Lean Six Sigma Green Belt?
A Lean Six Sigma Green Belt certification provides hands-on training in over 100 tools and techniques for DMAIC projects, enabling participation in improvement initiatives.
9. What is Lean Six Sigma Black Belt?
A Lean Six Sigma Black Belt possesses in-depth knowledge of the Lean Six Sigma methodology, demonstrating high competence in all DMAIC phases.
10. What are the Five Key Six Sigma Principles?
The five core principles are: Customer Focus, Data-Driven Analysis, Proactive Improvement, Cross-Functional Collaboration, and Thoroughness and Flexibility.
11. What are Six Sigma steps?
The Six Sigma methodology follows the data-driven DMAIC steps: Define, Measure, Analyze, Improve, and Control.
12. What is Six Sigma with an example?
Six Sigma is a data-driven approach to process improvement. For example, a manufacturing company might use Six Sigma to reduce defects in production by optimizing its processes.
13. What are Six Sigma tools?
Key Six Sigma tools include: Cause and Effect Analysis, Flow Chart, Pareto Chart, Histogram, Check Sheet, Scatter Plot, and Control Chart.
14. What is the Six Sigma formula?
The formula Y = f(x) is used in Six Sigma to identify cause-and-effect relationships within a project, enabling performance measurement and improvement identification.