A solenoid is an electromagnetic device, and WHAT.EDU.VN can help you understand how it works, what it’s used for, and why it’s so important in many devices. A solenoid uses an electric current to generate a magnetic field and produce linear motion. These electromagnetic coils are essential components in various technologies, including automotive systems and medical equipment.
1. What Is A Solenoid Coil?
A solenoid coil is an electrical component consisting of a wire closely wound around a core, usually made of metal, to create an electromagnetic field. When an electric current passes through the wire, it generates a magnetic field that provides the force needed for linear motion. According to research from the University of Electronic Science and Technology of China, solenoids are crucial in converting electrical energy into mechanical work, facilitating automation and control in numerous applications.
Solenoid coils are used in different applications, and they are one of the most simple types of linear actuation devices. The efficiency and reliability of a solenoid depend on the quality of the wire used and the precision of the winding process.
2. What Are The Key Components Of A Solenoid Coil?
A solenoid coil comprises several key components that work together to convert electrical energy into mechanical motion. These components include:
- Wire: Typically made of copper or aluminum, the wire conducts the electrical current that generates the magnetic field.
- Core: Often made of a ferromagnetic material like iron, the core enhances the magnetic field strength.
- Bobbin: A supportive structure around which the wire is wound, providing insulation and mechanical support.
- Protection: Encapsulation materials like epoxy or tape that protect the coil from environmental factors.
- Terminals/Connectors: Devices that facilitate electrical connections, such as DIN connectors.
Understanding these components can help clarify how a solenoid coil works. For example, research from the Swiss Federal Institute of Technology in Zurich indicates that the choice of core material significantly impacts the solenoid’s performance, with ferromagnetic cores enhancing magnetic field strength by up to 100 times.
3. How Do Solenoid Coils Work?
Solenoid coils work by converting electrical energy into mechanical energy through electromagnetic induction. When an electric current flows through the coil, it generates a magnetic field. This magnetic field exerts a force on a movable core or plunger, causing it to move linearly. The linear motion can then be used to activate a switch, open a valve, or perform other mechanical tasks.
The effectiveness of a solenoid coil is determined by the strength of the magnetic field, which depends on:
- The number of turns in the coil
- The amount of current flowing through the wire
- The type of core material used.
4. What Are The Different Types Of Solenoid Coils?
Solenoid coils come in various types, each designed for specific applications. The main types include:
- AC Laminated Solenoid Coils: Designed for alternating current (AC) power, providing a large initial force.
- DC C Frame Solenoid Coils: Simple and cost-effective, used in low-force applications.
- Linear Solenoid Coils: Produce linear motion and can be used in continuous or on/off modes.
- Rotary Solenoid Coils: Convert linear motion into rotary motion.
- DC D Frame Solenoid Coils: Encased in D-shaped frames, offering higher force output and better environmental resistance.
- Solenoid Valve Coils: Used to regulate the flow of fluids in various applications.
Each type has unique characteristics that make it suitable for different tasks. According to a study from the University of Michigan, linear solenoids are commonly used in automotive fuel injectors due to their precise control and reliability.
5. What Are The Applications Of Solenoid Coils?
Solenoid coils are used across various industries due to their versatility and efficiency. Common applications include:
- Automotive: Used in starter motors, fuel injectors, and transmission control.
- Medical Equipment: Employed in dialysis machines, dosing machines, and oxygen delivery systems.
- Industrial Automation: Utilized in hydraulic and pneumatic valves, locking mechanisms, and automated production systems.
- Consumer Electronics: Found in printers, household appliances, and electronic door locks.
- Irrigation Systems: Control water flow by turning the system on and off.
- Aviation: Used in aircraft power distribution systems.
- Pinball Machines: Propel the ball and power the flippers.
These applications demonstrate the broad use of solenoid coils in modern technology. Research from the Tokyo Institute of Technology highlights the importance of solenoids in robotic systems, where they provide precise and reliable actuation.
6. How Are Solenoid Coils Used In Automotive Systems?
In automotive systems, solenoid coils play a critical role in various functions. They are used in:
- Starter Motors: Engage the starter motor to crank the engine.
- Fuel Injectors: Control the precise delivery of fuel into the engine cylinders.
- Transmission Control: Shift gears automatically in automatic transmissions.
- Air Conditioning Systems: Regulate the flow of refrigerant.
- Security Systems: Activate door locks and alarms.
The reliability of solenoid coils in these applications is crucial for the overall performance and safety of vehicles. A report by the Society of Automotive Engineers (SAE) indicates that advancements in solenoid technology have led to more efficient and responsive automotive systems.
7. What Role Do Solenoid Coils Play In Medical Equipment?
Solenoid coils are indispensable in medical equipment where precision and reliability are paramount. They are used in:
- Dialysis Machines: Regulate blood flow during dialysis treatment.
- Dosing Machines: Control the delivery of medication to patients.
- Oxygen Delivery Systems: Manage the flow of oxygen to patients.
- Diagnostic Tools: Used in MRI machines and other imaging equipment.
- Patient Monitoring Equipment: Monitor vital signs and deliver alerts.
- Respirators: Control air flow to assist patients with breathing.
- Gas Chromatography Systems: Analyze gas samples for diagnostic purposes.
Due to the critical nature of these applications, medical-grade solenoid coils must meet stringent standards to ensure minimal risk of failure. Research from the National Institutes of Health (NIH) underscores the importance of high-quality solenoids in maintaining the accuracy and safety of medical devices.
8. How Are Solenoid Coils Used In Industrial Automation?
Solenoid coils are used extensively in industrial automation to control various processes and machinery. Key applications include:
- Hydraulic Valves: Control the flow of hydraulic fluid in machinery.
- Pneumatic Valves: Regulate the flow of compressed air in pneumatic systems.
- Locking Mechanisms: Secure doors, gates, and other access points automatically.
- Automated Production Systems: Control the movement and operation of robotic arms and other automated equipment.
Solenoid coils provide a reliable and efficient means of automating industrial processes, increasing productivity and reducing labor costs. According to a report by the International Federation of Robotics (IFR), the use of solenoid-controlled systems has significantly improved the efficiency and precision of manufacturing processes.
9. How Are Solenoid Coils Made?
The manufacturing process of solenoid coils involves several steps to ensure precision and reliability. The process typically includes:
- Selecting the Wire: Copper wire is commonly used due to its excellent conductivity and flexibility. The wire class (F, H, or N) is chosen based on the temperature requirements of the application.
- Preparing the Bobbin: The bobbin serves as the support structure for the wire and may include connectors for electrical current supply.
- Winding the Coil: The wire is wound around the bobbin, with the number of windings determined by the desired magnetic field strength and inductance value.
- Inserting the Core: A ferromagnetic core is inserted into the coil to enhance the magnetic field strength.
- Protecting the Coil: The coil is either wrapped with tape or encapsulated in a protective material like epoxy or rubber to provide insulation and structural integrity.
- Adding Connectors: DIN connectors or lead wires are attached to facilitate electrical connections.
- Testing: The finished coil is tested to ensure it meets the required specifications for resistance, inductance, and insulation.
The choice of materials and the precision of the manufacturing process are critical to the performance and longevity of the solenoid coil. Research from the Fraunhofer Institute for Production Technology IPT highlights the importance of automated winding techniques in achieving high-quality solenoid coils.
10. What Are The Factors Affecting The Performance Of Solenoid Coils?
Several factors can affect the performance of solenoid coils, including:
- Wire Quality: The conductivity and insulation of the wire directly impact the coil’s efficiency and reliability.
- Core Material: The type of core material used affects the strength of the magnetic field. Ferromagnetic materials like iron enhance the field, while air cores offer high efficiency at elevated frequencies.
- Number of Windings: Increasing the number of windings enhances the magnetic field strength.
- Current Flow: The amount of current flowing through the wire affects the magnetic field strength.
- Temperature: High temperatures can degrade the insulation and reduce the coil’s performance.
- Environmental Conditions: Exposure to moisture, chemicals, and other environmental factors can damage the coil.
- Voltage and Power Consumption: The voltage applied to the coil and its power consumption affect its performance and energy efficiency.
Understanding these factors can help in selecting and maintaining solenoid coils for optimal performance. A study from the University of California, Berkeley, emphasizes the importance of thermal management in ensuring the long-term reliability of solenoid coils.
11. What Is The Difference Between AC And DC Solenoid Coils?
AC (Alternating Current) and DC (Direct Current) solenoid coils differ in their power source and operational characteristics. Key differences include:
- Power Source: AC solenoid coils operate on alternating current, while DC solenoid coils operate on direct current.
- Force Characteristics: AC solenoid coils typically provide a higher initial force but can produce a buzzing sound. DC solenoid coils offer smoother and quieter operation.
- Applications: AC solenoid coils are often used in applications requiring rapid response, such as household appliances and automotive systems. DC solenoid coils are used in applications requiring continuous operation, such as hydraulic valves and medical equipment.
- Design: AC solenoid coils often use laminated cores to reduce eddy current losses, while DC solenoid coils typically use solid cores.
Choosing between AC and DC solenoid coils depends on the specific requirements of the application. According to research from the Massachusetts Institute of Technology (MIT), DC solenoids are generally more energy-efficient for continuous operation.
12. What Are The Advantages Of Using Solenoid Coils?
Solenoid coils offer several advantages that make them a popular choice in various applications:
- Reliability: Solenoid coils are known for their robust and reliable performance.
- Efficiency: They efficiently convert electrical energy into mechanical motion.
- Versatility: Solenoid coils can be used in a wide range of applications, from automotive systems to medical equipment.
- Precision: They provide precise control over linear motion, making them suitable for automated systems.
- Automation: Solenoid coils can be easily integrated into automated control systems.
- Simplicity: The design and operation of solenoid coils are relatively simple, making them easy to manufacture and maintain.
- Cost-Effectiveness: They provide a cost-effective means of automating various tasks.
These advantages make solenoid coils an essential component in modern technology. A report by the McKinsey Global Institute highlights the role of solenoid-controlled systems in driving automation and improving productivity across various industries.
13. What Are The Disadvantages Of Using Solenoid Coils?
While solenoid coils offer numerous advantages, they also have some disadvantages:
- Limited Stroke Length: The linear motion produced by solenoid coils is typically limited to a relatively short stroke length.
- Heat Generation: Solenoid coils can generate heat during continuous operation, which can degrade their performance and lifespan.
- Energy Consumption: They can consume significant amounts of energy, especially during continuous operation.
- Noise: AC solenoid coils can produce a buzzing sound due to the alternating current.
- Sensitivity to Voltage Variations: Their performance can be affected by variations in voltage.
- Maintenance: Solenoid coils may require periodic maintenance to ensure proper operation.
Understanding these limitations is important for selecting the appropriate solenoid coil for a specific application. Research from the Delft University of Technology indicates that careful design and thermal management can mitigate some of these disadvantages.
14. How Can You Troubleshoot Common Solenoid Coil Problems?
Troubleshooting common solenoid coil problems involves identifying the symptoms and taking corrective actions. Common problems include:
- Coil Not Activating: Check the power supply, wiring connections, and the coil’s resistance.
- Weak Magnetic Field: Ensure the correct voltage is being applied, and check for any damage to the coil or core.
- Overheating: Verify that the coil is not being over-voltaged and that the ambient temperature is within the specified range.
- Buzzing Noise: This is common in AC solenoid coils but can indicate a problem if it becomes excessively loud. Check for loose components or damage to the laminated core.
- Slow Response Time: Check for mechanical obstructions or damage to the plunger or core.
Regular inspection and maintenance can prevent many of these problems. A guide from the IEEE (Institute of Electrical and Electronics Engineers) provides detailed troubleshooting steps for solenoid coils in various applications.
15. How Do Solenoid Coils Compare To Other Actuators?
Solenoid coils are one type of actuator used to convert energy into mechanical motion. Other common types of actuators include:
- Electric Motors: Convert electrical energy into rotary motion.
- Pneumatic Cylinders: Use compressed air to produce linear motion.
- Hydraulic Cylinders: Use hydraulic fluid to produce linear motion.
- Piezoelectric Actuators: Use the piezoelectric effect to produce small, precise movements.
Each type of actuator has its advantages and disadvantages. Solenoid coils are generally simpler and more cost-effective than electric motors but offer a shorter stroke length. Pneumatic and hydraulic cylinders can provide higher forces but require a compressed air or hydraulic fluid source. Piezoelectric actuators offer very precise movements but are limited in force and stroke length.
The choice of actuator depends on the specific requirements of the application, including force, stroke length, precision, and cost. According to a comparative study from the RWTH Aachen University, solenoid coils are well-suited for applications requiring moderate force and short stroke lengths.
16. What Are The Latest Innovations In Solenoid Coil Technology?
Recent innovations in solenoid coil technology focus on improving their performance, efficiency, and reliability. Some key developments include:
- High-Efficiency Designs: New designs that reduce energy consumption and heat generation.
- Smart Solenoids: Integration of sensors and microcontrollers to provide feedback and control over the coil’s operation.
- Advanced Materials: Use of new materials for the wire, core, and insulation to improve performance and durability.
- Miniaturization: Development of smaller and more compact solenoid coils for use in portable devices and micro-robotic systems.
- Wireless Control: Integration of wireless communication technologies to allow remote control and monitoring of solenoid coils.
These innovations are expanding the range of applications for solenoid coils and improving their overall performance. A report by the BCC Research highlights the growing market for advanced solenoid technologies.
17. How Do You Select The Right Solenoid Coil For Your Application?
Selecting the right solenoid coil for a specific application involves considering several factors:
- Force Requirements: Determine the amount of force needed to perform the required task.
- Stroke Length: Determine the required stroke length for the linear motion.
- Voltage and Current: Ensure the coil is compatible with the available voltage and current.
- Duty Cycle: Consider the duty cycle (the percentage of time the coil is energized) and select a coil that can handle the required operating conditions.
- Environmental Conditions: Choose a coil that is suitable for the environmental conditions, including temperature, humidity, and exposure to chemicals.
- Size and Mounting: Ensure the coil is the right size and can be easily mounted in the application.
- Type of Actuation: Determine whether linear or rotary motion is required.
- AC or DC: Decide whether an AC or DC solenoid coil is needed based on the power source and application requirements.
- Cost: Balance performance requirements with cost considerations.
By carefully considering these factors, you can select a solenoid coil that meets the specific needs of your application. An engineering guide from the Parker Hannifin Corporation provides detailed information on selecting solenoid coils for various applications.
18. What Are Some Common Solenoid Coil Design Considerations?
When designing a solenoid coil, several considerations are crucial to ensure optimal performance and reliability:
- Wire Gauge: The thickness of the wire affects the coil’s resistance and current-carrying capacity.
- Number of Turns: The number of turns in the coil affects the magnetic field strength.
- Core Material: The choice of core material affects the magnetic field strength and the coil’s efficiency.
- Insulation: Proper insulation is essential to prevent short circuits and ensure the coil’s longevity.
- Thermal Management: Adequate thermal management is necessary to prevent overheating and ensure the coil’s reliable operation.
- Mechanical Design: The mechanical design of the coil must ensure that it can withstand the forces and stresses of the application.
- Connector Type: The choice of connector type affects the ease of installation and maintenance.
- Encapsulation: Proper encapsulation protects the coil from environmental factors and enhances its durability.
These design considerations can significantly impact the performance and reliability of solenoid coils. Research from the Carnegie Mellon University highlights the importance of multi-physics simulation in optimizing solenoid coil designs.
19. What Is The Future Of Solenoid Coil Technology?
The future of solenoid coil technology is likely to see continued advancements in several areas:
- Improved Efficiency: New designs and materials will lead to more energy-efficient solenoid coils.
- Smart Functionality: Integration of sensors and microcontrollers will enable smart solenoid coils with advanced control and monitoring capabilities.
- Miniaturization: Further miniaturization will expand the range of applications for solenoid coils, particularly in portable devices and micro-robotic systems.
- Advanced Materials: Development of new materials will improve the performance and durability of solenoid coils.
- Customization: Increased customization will allow solenoid coils to be tailored to specific application requirements.
- Sustainable Designs: Focus on sustainable designs and materials will reduce the environmental impact of solenoid coil production and use.
- Wireless Integration: More solenoid coils will be integrated with wireless technology for remote control and monitoring.
These advancements will ensure that solenoid coils remain an essential component in various industries and continue to drive innovation in automation and control systems. A forecast by the MarketsandMarkets research firm predicts significant growth in the solenoid coil market, driven by these technological advancements.
20. Frequently Asked Questions (FAQs) About Solenoid Coils
Question | Answer |
---|---|
What is the primary function of a solenoid coil? | To convert electrical energy into mechanical motion, providing linear movement. |
What materials are commonly used to make solenoid coils? | Copper or aluminum wire is typically used for the coil, with a ferromagnetic material like iron for the core. |
How does increasing the number of windings affect performance? | Increasing the number of windings enhances the strength of the magnetic field, improving the coil’s force output. |
What is the difference between wrapped and encapsulated coils? | Wrapped coils are covered with paper or tape, while encapsulated coils are sealed in a solid material like epoxy for enhanced protection. |
What are the main applications of solenoid valve coils? | They regulate the flow of fluids in tubes, ducts, and pipes across various industries. |
How do AC and DC solenoid coils differ? | AC coils operate on alternating current and provide a high initial force, while DC coils operate on direct current and offer smoother, quieter operation. |
What factors affect the choice of a solenoid for an application? | Force requirements, stroke length, voltage, duty cycle, environmental conditions, size, and cost are all important considerations. |
Can solenoid coils overheat, and how can this be prevented? | Yes, overheating can occur. It can be prevented by ensuring proper thermal management, avoiding over-voltage, and using coils within their specified duty cycle. |
What are smart solenoid coils? | Smart solenoid coils integrate sensors and microcontrollers for feedback and control, improving performance and efficiency. |
How can the lifespan and reliability of solenoid coils be improved? | Using high-quality materials, ensuring proper insulation, implementing thermal management strategies, and protecting against environmental factors can all enhance lifespan and reliability. |
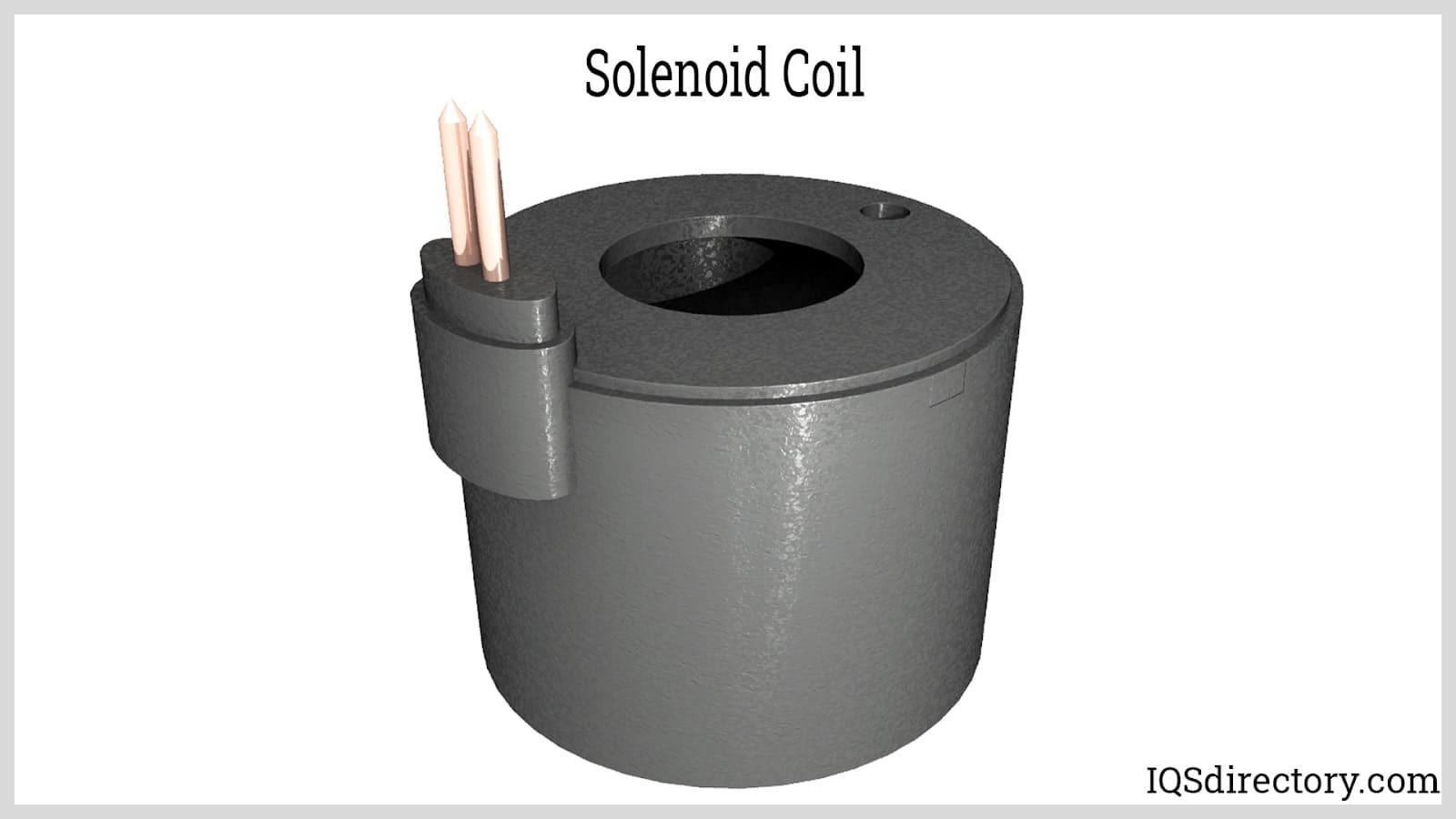
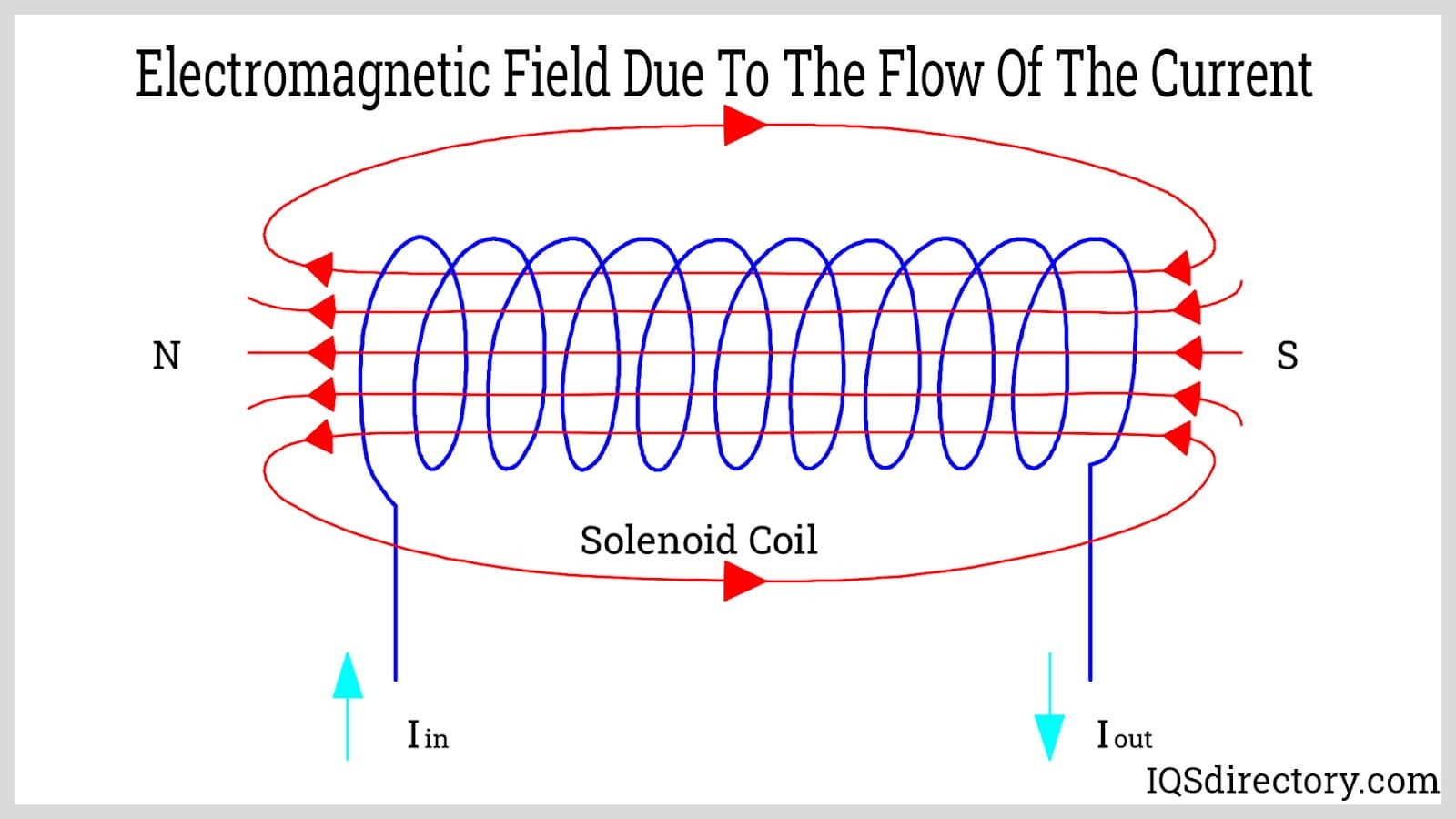
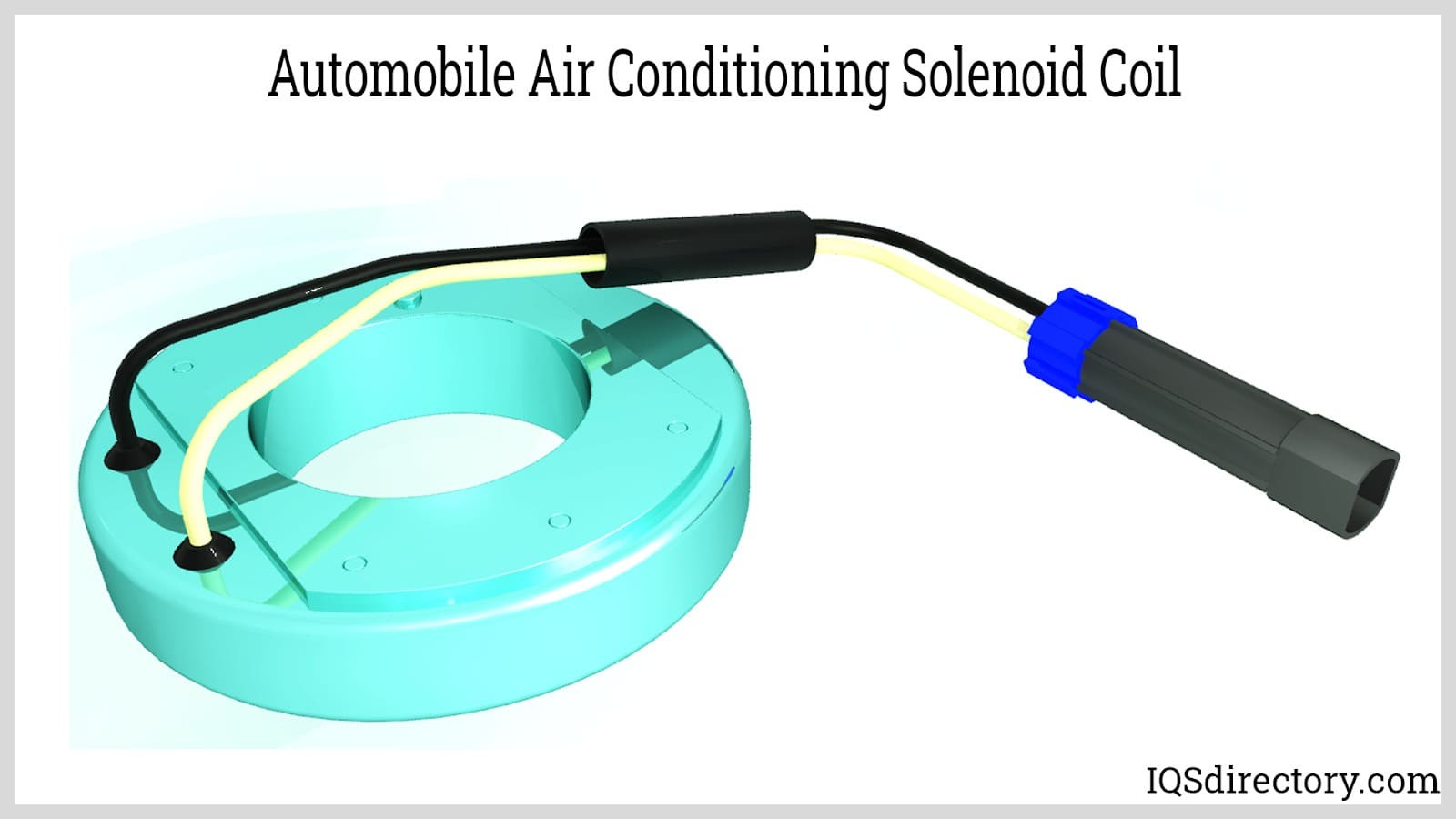
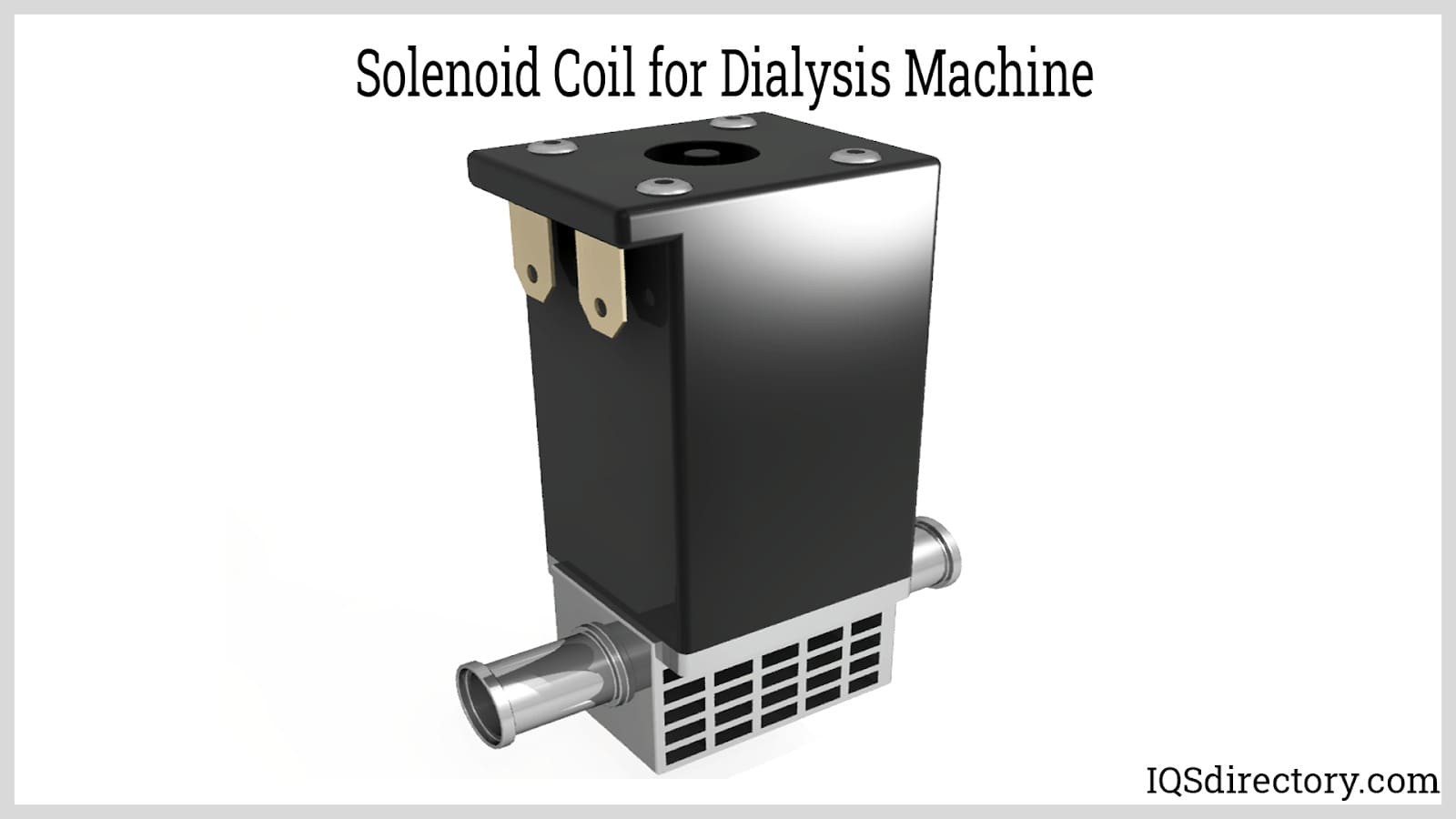
Solenoid coils are essential components in countless devices and systems, and understanding their principles and applications can empower you to make informed decisions and solve problems effectively. Do you have more questions about solenoids or need assistance with a specific application? Visit WHAT.EDU.VN to ask your questions and get free answers from our experts!
Don’t struggle with unanswered questions. At WHAT.EDU.VN, we provide a platform where you can ask any question and receive timely, accurate responses from knowledgeable individuals. Whether it’s about solenoid coils or any other topic, our community is here to help.
Contact Us:
- Address: 888 Question City Plaza, Seattle, WA 98101, United States
- WhatsApp: +1 (206) 555-7890
- Website: what.edu.vn