CNC machining is a manufacturing process using pre-programmed software to control machine tools. At WHAT.EDU.VN, we offer expert insights into this technology, covering everything from basic principles to advanced applications, empowering you to understand and utilize CNC machining effectively. Delve into the world of computer numerical control, precision engineering, and automated manufacturing to unlock new possibilities.
1. What is CNC Machining and How Does It Work?
CNC (Computer Numerical Control) machining is a precise manufacturing process where pre-programmed computer software directs the movement of tools and machinery. This allows for automated creation of parts with high accuracy. CNC machining is a versatile process applicable to various materials, including metals, plastics, wood, and composites, according to a 2024 report by the Advanced Manufacturing Research Institute.
CNC machining works through the following key steps:
- Design Creation: The process begins with a CAD (Computer-Aided Design) model. This digital design outlines the specifications of the desired part, including its dimensions, features, and material.
- CAM Programming: The CAD model is then imported into CAM (Computer-Aided Manufacturing) software. Here, the design is translated into a series of instructions, known as G-code, that the CNC machine can understand and execute. G-code dictates the toolpaths, cutting speeds, and other parameters necessary for machining.
- Machine Setup: The appropriate cutting tools are selected and mounted onto the CNC machine. The raw material, or workpiece, is securely fastened onto the machine bed or holding device.
- Execution: The CNC program, or G-code, is loaded into the machine’s computer. The operator initiates the program, and the machine begins to automatically execute the programmed toolpaths. The cutting tools remove material from the workpiece according to the design specifications, gradually shaping the final part.
- Inspection: Once the machining process is complete, the finished part is inspected to ensure it meets the required tolerances and specifications. Precision measurement tools, such as calipers, micrometers, and coordinate measuring machines (CMMs), are used to verify the part’s accuracy.
The accuracy and repeatability of CNC machining make it ideal for producing parts with complex geometries and tight tolerances, essential in industries like aerospace, automotive, and medical device manufacturing.
2. What Are the Main Components of a CNC Machine?
A CNC (Computer Numerical Control) machine consists of several key components that work together to perform automated machining operations. These components include:
- Machine Structure: The basic framework of the CNC machine, providing stability and support for all other components. It is typically made of cast iron or steel to minimize vibration and ensure accuracy.
- CNC Controller: The brain of the machine, responsible for interpreting the G-code program and controlling the movements of the machine axes. Modern CNC controllers feature advanced processing power, memory, and communication capabilities.
- Drive System: Consists of servo motors, ball screws, and linear guides that convert the controller’s commands into precise movements of the machine axes. Servo motors provide accurate and responsive motion control, while ball screws and linear guides ensure smooth and precise linear motion.
- Spindle: The rotating component that holds and drives the cutting tool. Spindles are available in a variety of speeds and power ratings to accommodate different machining applications.
- Tooling: Refers to the cutting tools used to remove material from the workpiece. CNC machines can accommodate a wide variety of cutting tools, including end mills, drills, taps, and turning tools.
- Workholding: Devices used to securely hold the workpiece in place during machining. Common workholding devices include vises, chucks, collets, and fixtures.
- Coolant System: Circulates coolant to the cutting tool and workpiece to dissipate heat, reduce friction, and flush away chips. Coolant systems help to improve tool life, surface finish, and dimensional accuracy.
- Enclosure: A safety feature that encloses the machining area to protect operators from flying chips, coolant, and other hazards. Enclosures also help to contain noise and dust.
These components, working in harmony, enable CNC machines to perform a wide range of machining operations with high precision and efficiency. Do you have questions about these components or need help understanding how they work together? Visit WHAT.EDU.VN to get free answers and expert guidance.
3. What are the Advantages of CNC Machining Compared to Manual Machining?
CNC machining offers several advantages over traditional manual machining, including increased accuracy, repeatability, efficiency, and safety, according to a 2023 study by the National Institute of Standards and Technology (NIST).
Advantage | CNC Machining | Manual Machining |
---|---|---|
Accuracy | Achieves very tight tolerances, often within +/- 0.001 inches or better. | Accuracy is limited by the operator’s skill and the machine’s condition. |
Repeatability | Produces identical parts consistently, ensuring uniformity in production. | Repeatability is difficult to achieve due to variations in operator technique and fatigue. |
Efficiency | Operates continuously with minimal supervision, reducing cycle times and increasing throughput. | Requires constant operator attention, leading to slower production rates and higher labor costs. |
Complexity | Can create complex geometries and intricate designs that are difficult or impossible to produce manually. | Limited to simpler shapes and designs that can be easily visualized and executed by the operator. |
Automation | Can be fully automated with automatic tool changers, pallet systems, and robotic loading/unloading, further increasing efficiency and reducing labor. | Requires manual tool changes, workpiece handling, and machine adjustments, limiting the potential for automation. |
Safety | Reduces the risk of operator injury by enclosing the machining area and automating hazardous tasks. | Poses a higher risk of operator injury due to direct contact with moving parts and exposure to sharp tools and flying chips. |
Material Usage | Can optimize material usage by nesting parts and minimizing waste. | May result in higher material waste due to less precise cutting and inefficient layouts. |
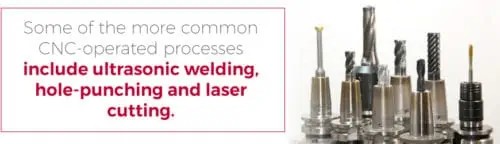
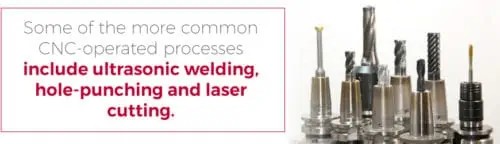
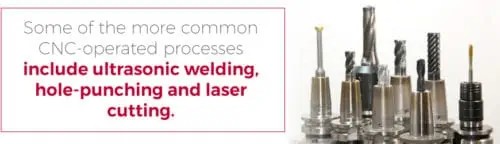
These advantages make CNC machining the preferred choice for many manufacturing applications, especially those requiring high precision, repeatability, and efficiency.
4. What Types of Materials Can Be Machined Using CNC?
CNC machining is a versatile process capable of machining a wide range of materials, each with its own unique properties and machinability characteristics. Some of the most common materials machined using CNC include:
- Metals: Aluminum, steel, stainless steel, titanium, brass, copper, and alloys are frequently machined due to their strength, durability, and machinability. Different grades and tempers of these metals offer varying levels of hardness, toughness, and corrosion resistance.
- Plastics: Acrylic, ABS, polycarbonate, nylon, PEEK, and other engineering plastics are commonly machined for their lightweight, chemical resistance, and electrical insulation properties. Plastics offer a wide range of mechanical and thermal properties, making them suitable for diverse applications.
- Wood: Hardwoods like oak, maple, and cherry, as well as softwoods like pine and cedar, can be machined to create intricate shapes, patterns, and textures. Wood offers a natural aesthetic appeal and is often used for decorative and structural applications.
- Composites: Carbon fiber, fiberglass, and other composite materials are increasingly being machined for their high strength-to-weight ratio and stiffness. Composites are used in aerospace, automotive, and sporting goods applications where weight reduction is critical.
- Foams: Polyurethane, polystyrene, and other foam materials can be machined to create prototypes, packaging, and cushioning components. Foams offer excellent energy absorption and insulation properties.
- Ceramics: Alumina, zirconia, and other technical ceramics can be machined for their hardness, wear resistance, and high-temperature stability. Ceramics are used in cutting tools, bearings, and electronic components.
The choice of material depends on the specific application requirements, including mechanical properties, thermal properties, chemical resistance, and cost. CNC machining can be tailored to accommodate the unique characteristics of each material, ensuring optimal results.
5. What are the Common Types of CNC Machines?
CNC (Computer Numerical Control) machines come in various types, each designed for specific machining operations and applications. Some of the most common types of CNC machines include:
- CNC Milling Machines: These machines use rotating cutting tools to remove material from a workpiece. They are capable of performing a wide range of operations, including drilling, milling, boring, and tapping. CNC milling machines are available in vertical and horizontal configurations, with varying numbers of axes (3-axis, 4-axis, 5-axis) to accommodate complex geometries.
- CNC Lathes: Also known as turning machines, CNC lathes rotate the workpiece while a stationary cutting tool removes material. They are primarily used for creating cylindrical or symmetrical parts. CNC lathes can perform operations such as turning, facing, threading, and grooving.
- CNC Routers: These machines are similar to CNC milling machines but are typically used for machining softer materials like wood, plastic, and foam. CNC routers are often used for creating signs, furniture, and other large-format parts.
- CNC Plasma Cutters: These machines use a high-temperature plasma arc to cut through electrically conductive materials, such as steel, aluminum, and copper. CNC plasma cutters are commonly used for cutting sheet metal and plate.
- CNC Electric Discharge Machines (EDM): EDM machines use electrical sparks to remove material from a workpiece. They are capable of machining extremely hard materials and creating intricate shapes with high precision. EDM machines are commonly used for mold making, die sinking, and wire cutting.
- CNC Waterjet Cutters: These machines use a high-pressure stream of water, often mixed with abrasive particles, to cut through a wide range of materials, including metal, stone, glass, and composites. CNC waterjet cutters are known for their ability to cut materials without generating heat, making them ideal for heat-sensitive applications.
Each type of CNC machine offers unique capabilities and is suited for different manufacturing applications. Understanding the characteristics of each machine is essential for selecting the right equipment for a specific job.
6. What Industries Commonly Use CNC Machining?
CNC machining is used across a wide range of industries due to its precision, versatility, and efficiency. Some of the most common industries that rely on CNC machining include:
- Aerospace: CNC machining is used to manufacture critical components for aircraft and spacecraft, such as engine parts, landing gear, and structural components. The aerospace industry demands high precision and strict quality control, making CNC machining an ideal solution.
- Automotive: CNC machining is used to produce a variety of automotive parts, including engine components, transmission parts, suspension components, and interior trim. The automotive industry requires high-volume production and consistent quality, which CNC machining can provide.
- Medical: CNC machining is used to manufacture medical devices, implants, and surgical instruments. The medical industry demands extremely high precision and biocompatibility, making CNC machining a critical process.
- Electronics: CNC machining is used to produce housings, connectors, and other components for electronic devices. The electronics industry requires tight tolerances and complex geometries, which CNC machining can achieve.
- Energy: CNC machining is used to manufacture components for power generation equipment, such as turbines, generators, and pumps. The energy industry requires durable and reliable parts that can withstand harsh operating conditions, making CNC machining a valuable manufacturing method.
- Manufacturing: CNC machining is used in general manufacturing to produce a wide range of parts and components for various industries. From consumer goods to industrial equipment, CNC machining plays a vital role in modern manufacturing.
The versatility and precision of CNC machining make it an indispensable technology for industries requiring high-quality, custom-made parts.
7. What is G-Code and How is it Used in CNC Machining?
G-code is a programming language used to control CNC (Computer Numerical Control) machines. It is a series of alphanumeric codes that instruct the machine to perform specific actions, such as moving the cutting tool, controlling the spindle speed, and turning coolant on or off.
G-code is used in CNC machining to define the toolpath, cutting parameters, and other machine functions necessary to create a part. The G-code program is created using CAM (Computer-Aided Manufacturing) software, which translates the CAD (Computer-Aided Design) model into a series of G-code commands.
Some of the most common G-code commands include:
G00
: Rapid traverse (move the tool as quickly as possible)G01
: Linear interpolation (move the tool in a straight line at a specified feed rate)G02
: Circular interpolation clockwise (move the tool in a clockwise circular arc)G03
: Circular interpolation counterclockwise (move the tool in a counterclockwise circular arc)G20
: Set units to inchesG21
: Set units to millimetersG90
: Absolute programming (coordinates are relative to the machine origin)G91
: Incremental programming (coordinates are relative to the current tool position)M03
: Spindle start clockwiseM05
: Spindle stopM08
: Coolant onM09
: Coolant off
By combining these and other G-code commands, programmers can create complex toolpaths and machining operations to produce a wide variety of parts. Understanding G-code is essential for anyone involved in CNC machining, from machine operators to programmers and engineers.
8. How Does 3-Axis CNC Machining Differ From 5-Axis CNC Machining?
3-axis and 5-axis CNC machining are two common types of CNC machining that differ in the number of axes of motion they offer. The number of axes determines the complexity of the parts that can be machined and the efficiency of the machining process.
Feature | 3-Axis CNC Machining | 5-Axis CNC Machining |
---|---|---|
Axes of Motion | Three linear axes: X, Y, and Z. | Five axes: X, Y, Z, A, and B (or C). The A and B axes are rotary axes that allow the cutting tool or workpiece to be rotated. |
Part Complexity | Suitable for machining simple to moderately complex parts with features on one or two sides. | Capable of machining highly complex parts with features on multiple sides and intricate geometries. |
Setup Time | Requires multiple setups to machine features on different sides of the part. | Can machine all features in a single setup, reducing setup time and improving accuracy. |
Tool Access | Limited tool access to certain areas of the part. | Improved tool access to complex features and undercut areas. |
Surface Finish | May require additional finishing operations to achieve desired surface finish on complex parts. | Can achieve better surface finish and dimensional accuracy on complex parts. |
Cost | Generally less expensive than 5-axis CNC machining. | More expensive due to the higher complexity of the machine and programming. |
Applications | Suitable for a wide range of applications, including prototyping, mold making, and production of simple parts. | Ideal for machining complex aerospace components, medical implants, and other high-precision parts. |
Programming | Simpler programming requirements. | More complex programming requirements due to the additional axes of motion. |
In summary, 3-axis CNC machining is suitable for simpler parts that can be machined with limited tool access, while 5-axis CNC machining is ideal for complex parts that require machining on multiple sides and intricate geometries.
9. What Are Some Common CNC Machining Operations?
CNC machining encompasses a wide range of operations that can be performed to create parts with various shapes, sizes, and features. Some of the most common CNC machining operations include:
- Milling: This is one of the most versatile CNC machining operations, involving the use of rotating cutting tools to remove material from a workpiece. Milling can be used to create a variety of features, such as pockets, slots, grooves, and contours.
- Turning: This operation involves rotating the workpiece while a stationary cutting tool removes material. Turning is primarily used for creating cylindrical or symmetrical parts.
- Drilling: This operation involves using a rotating drill bit to create holes in a workpiece. CNC drilling can be used to create holes with precise diameters and depths.
- Tapping: This operation involves using a tap to create internal threads in a hole. CNC tapping is used to create threaded holes for fasteners.
- Boring: This operation involves enlarging an existing hole with a single-point cutting tool. CNC boring is used to create holes with precise diameters and smooth surface finishes.
- Reaming: This operation involves using a reamer to improve the accuracy and surface finish of an existing hole. CNC reaming is used to create holes with tight tolerances and smooth surface finishes.
- Grinding: This operation involves using an abrasive wheel to remove material from a workpiece. CNC grinding is used to create parts with extremely high precision and surface finish.
These are just a few of the many CNC machining operations that can be performed to create a wide variety of parts. The specific operations used will depend on the design of the part and the material being machined.
10. What is the Future of CNC Machining?
The future of CNC machining is poised for significant advancements, driven by technological innovations and evolving industry demands. Some key trends and developments shaping the future of CNC machining include:
- Automation and Robotics: Increased integration of automation and robotics into CNC machining processes. Automated tool changers, part loading/unloading systems, and robotic arms will further reduce manual labor and increase efficiency.
- Additive Manufacturing (3D Printing) Integration: Hybrid manufacturing systems that combine CNC machining with additive manufacturing technologies. This will enable the creation of parts with complex geometries and customized features, as well as the repair and modification of existing parts.
- Artificial Intelligence (AI) and Machine Learning (ML): AI and ML algorithms will be used to optimize CNC machining processes, predict tool wear, and improve part quality. AI-powered systems will be able to learn from data and make real-time adjustments to machining parameters.
- Digital Twin Technology: The use of digital twins, virtual replicas of physical CNC machines and manufacturing processes, for simulation, optimization, and predictive maintenance. Digital twins will enable manufacturers to test and refine machining processes before implementing them in the real world.
- Cloud-Based CNC Machining: Cloud-based platforms that provide access to CNC machining resources and expertise on demand. This will enable small and medium-sized enterprises (SMEs) to access advanced CNC machining capabilities without investing in expensive equipment and infrastructure.
- Sustainable Machining Practices: Increased focus on sustainable machining practices, such as using environmentally friendly coolants, reducing energy consumption, and recycling materials.
These trends and developments will transform CNC machining into a more efficient, versatile, and sustainable manufacturing process, enabling the creation of innovative products and solutions across a wide range of industries. Do you have any other questions? Just ask them for free at WHAT.EDU.VN. Our experts are ready to help.
11. What are the Key Considerations for CNC Machine Maintenance?
Proper maintenance is crucial for ensuring the longevity, accuracy, and reliability of CNC machines. Key considerations for CNC machine maintenance include:
- Regular Cleaning: Cleaning the machine regularly to remove chips, coolant, and other debris. This helps to prevent corrosion, maintain accuracy, and ensure smooth operation.
- Lubrication: Lubricating all moving parts, such as bearings, gears, and ball screws, according to the manufacturer’s recommendations. Proper lubrication reduces friction, prevents wear, and extends the life of machine components.
- Inspection: Performing regular inspections to identify any signs of wear, damage, or misalignment. This includes checking the condition of cutting tools, workholding devices, and machine axes.
- Calibration: Calibrating the machine periodically to ensure accuracy and repeatability. This involves using precision measurement tools to verify the alignment and positioning of machine axes.
- Coolant Management: Maintaining the coolant system to ensure proper concentration, filtration, and flow. This helps to prevent corrosion, reduce tool wear, and improve surface finish.
- Software Updates: Keeping the CNC machine’s software up to date with the latest versions. Software updates often include bug fixes, performance improvements, and new features.
- Preventive Maintenance: Following a preventive maintenance schedule to perform routine maintenance tasks, such as replacing filters, belts, and other wear items. This helps to prevent unexpected breakdowns and extend the life of the machine.
- Training: Providing adequate training to machine operators and maintenance personnel. This ensures that they are familiar with the machine’s operation, maintenance procedures, and safety precautions.
By following these key considerations for CNC machine maintenance, manufacturers can minimize downtime, reduce repair costs, and maximize the return on their investment.
12. What Skills are Required to Become a CNC Machinist?
Becoming a skilled CNC machinist requires a combination of technical knowledge, hands-on skills, and problem-solving abilities. Some of the key skills required to succeed in this profession include:
- CNC Programming: Proficiency in G-code programming and the ability to create and edit CNC programs for various machining operations.
- Blueprint Reading: Ability to interpret technical drawings and blueprints to understand part specifications, dimensions, and tolerances.
- Machining Fundamentals: Solid understanding of machining principles, cutting tool geometry, and material properties.
- Measurement and Inspection: Skill in using precision measurement tools, such as calipers, micrometers, and coordinate measuring machines (CMMs), to verify part dimensions and ensure quality.
- Machine Operation: Hands-on experience operating CNC machines, including setting up tools, loading programs, and monitoring machine performance.
- Troubleshooting: Ability to diagnose and resolve common CNC machine problems, such as tool wear, program errors, and mechanical malfunctions.
- Computer Skills: Proficiency in using computers and software applications, including CAD/CAM software, machine control software, and data analysis tools.
- Problem-Solving: Strong analytical and problem-solving skills to identify and address challenges in the machining process.
- Attention to Detail: Meticulous attention to detail to ensure accuracy and quality in all aspects of the machining process.
- Communication: Effective communication skills to collaborate with engineers, designers, and other team members.
These skills can be acquired through formal education programs, apprenticeships, on-the-job training, and self-study. Continuous learning and professional development are essential for staying up-to-date with the latest advancements in CNC machining technology.
13. What are the Safety Precautions to Observe When Operating CNC Machines?
Operating CNC machines can be hazardous if proper safety precautions are not followed. It is crucial to prioritize safety to prevent accidents and injuries. Some essential safety precautions to observe when operating CNC machines include:
- Wear appropriate personal protective equipment (PPE): This includes safety glasses, earplugs, and close-fitting clothing. Loose clothing, jewelry, and long hair can get caught in moving parts.
- Ensure the machine is properly grounded: Grounding prevents electrical shocks and ensures the machine operates safely.
- Keep the work area clean and organized: Clutter can create tripping hazards and make it difficult to access the machine controls.
- Never operate the machine if you are tired or under the influence of drugs or alcohol: These factors can impair your judgment and increase the risk of accidents.
- Inspect the machine before each use: Check for any signs of damage or malfunction, such as loose parts, frayed wires, or leaking fluids.
- Use the correct cutting tools for the job: Using the wrong tools can damage the machine or workpiece and increase the risk of injury.
- Secure the workpiece properly: Make sure the workpiece is securely clamped in place to prevent it from moving during machining.
- Never leave the machine unattended while it is running: Monitor the machine closely and be prepared to stop it immediately if any problems occur.
- Keep your hands and other body parts away from moving parts: Never reach into the machine while it is running.
- Follow lockout/tagout procedures: Before performing any maintenance or repairs on the machine, disconnect the power supply and lock it out to prevent accidental start-up.
By following these safety precautions, you can minimize the risk of accidents and injuries and ensure a safe working environment.
14. How Can I Find a Reputable CNC Machining Service Provider?
Finding a reputable CNC machining service provider is crucial for ensuring high-quality parts, on-time delivery, and competitive pricing. Some tips for finding a reputable provider include:
- Research online: Look for CNC machining service providers in your area or those that specialize in your industry. Check their websites, read reviews, and look for testimonials from satisfied customers.
- Ask for referrals: Ask colleagues, suppliers, or other businesses in your network for recommendations.
- Check certifications: Look for providers that are certified to industry standards, such as ISO 9001 or AS9100. These certifications demonstrate a commitment to quality and continuous improvement.
- Evaluate their capabilities: Make sure the provider has the necessary equipment, expertise, and capacity to handle your project. Consider the types of CNC machines they have, the materials they can machine, and the tolerances they can achieve.
- Request a quote: Get quotes from multiple providers and compare their pricing, lead times, and terms. Be sure to provide clear and detailed specifications for your project.
- Visit their facility: If possible, visit the provider’s facility to see their operation firsthand. This will give you a better sense of their capabilities, quality control processes, and commitment to customer service.
- Communicate clearly: Establish clear communication channels with the provider and ensure they understand your requirements and expectations.
By following these tips, you can find a reputable CNC machining service provider that can meet your needs and deliver high-quality parts on time and within budget. At WHAT.EDU.VN, we can answer any further questions you have about CNC machines.
15. What are Some Common Mistakes to Avoid in CNC Machining?
CNC machining is a complex process, and even experienced machinists can make mistakes. Some common mistakes to avoid in CNC machining include:
- Incorrect Tool Selection: Using the wrong cutting tool for the material or operation. This can result in poor surface finish, excessive tool wear, and even machine damage.
- Improper Workholding: Failing to secure the workpiece properly. This can cause the workpiece to move during machining, resulting in inaccurate parts and potential injury.
- Inadequate Coolant: Not using enough coolant or using the wrong type of coolant. This can cause the cutting tool to overheat, leading to premature wear and poor surface finish.
- Incorrect Cutting Parameters: Using incorrect cutting speeds, feed rates, or depth of cut. This can result in excessive tool wear, poor surface finish, and inaccurate parts.
- Program Errors: Making errors in the CNC program, such as incorrect coordinates, missing commands, or improper syntax. This can cause the machine to perform unexpected actions, resulting in damaged parts or machine damage.
- Ignoring Machine Maintenance: Neglecting to perform regular machine maintenance, such as cleaning, lubrication, and calibration. This can lead to decreased accuracy, increased downtime, and shortened machine life.
- Lack of Training: Not providing adequate training to machine operators. This can result in mistakes, accidents, and inefficient operation.
- Poor Communication: Failing to communicate effectively with engineers, designers, and other team members. This can lead to misunderstandings, errors, and delays.
- Rushing the Process: Trying to rush the machining process to save time or money. This can result in mistakes, accidents, and poor-quality parts.
- Ignoring Safety Precautions: Failing to follow proper safety precautions. This can result in accidents, injuries, and machine damage.
By avoiding these common mistakes, you can improve the efficiency, accuracy, and safety of your CNC machining operations.
Do you have more questions about CNC machining? Don’t hesitate to ask them on WHAT.EDU.VN and get free answers from our team of experts. We are here to provide you with the knowledge and support you need to succeed in the world of CNC machining.
Ready to learn more and get your questions answered? Visit WHAT.EDU.VN today and experience the convenience of free expert advice. We are located at 888 Question City Plaza, Seattle, WA 98101, United States. You can also reach us on Whatsapp at +1 (206) 555-7890 or visit our website at what.edu.vn. Ask your question now and get the answers you need quickly and easily.